High-precision fully-automatic large transfer system
A fully automatic, high-precision technology, applied in the direction of manipulators, program-controlled manipulators, manufacturing tools, etc., can solve the problems of high technical difficulty, difficult positioning accuracy to meet high requirements, and no longer suitable, to achieve high positioning accuracy, The effect of high use value and reduced reprint time
- Summary
- Abstract
- Description
- Claims
- Application Information
AI Technical Summary
Problems solved by technology
Method used
Image
Examples
Embodiment Construction
[0022] The automatic transfer system is mainly composed of measurement unit 1, alignment unit 2, control unit 3, execution unit 4 and display unit 5. The block diagram of the system is shown in the attached figure 1 shown. The control unit 3 first controls the hydraulic regulating valve in the execution unit 4 according to the measurement data of the measurement unit 1, and drives the manipulator to run above the goods to be transferred. At this time, the alignment unit 2 measures the relative position coordinates of the manipulator and the goods in real time. Here At the same time, the control unit 3 is driven according to the real-time position coordinates so that the manipulator is constantly approaching the goods being transferred. During this process, the control unit 3 adjusts in real time through the data fed back by the sensors installed at each joint. The measurement results and various control information are sent to the display unit 5 for real-time display through t...
PUM
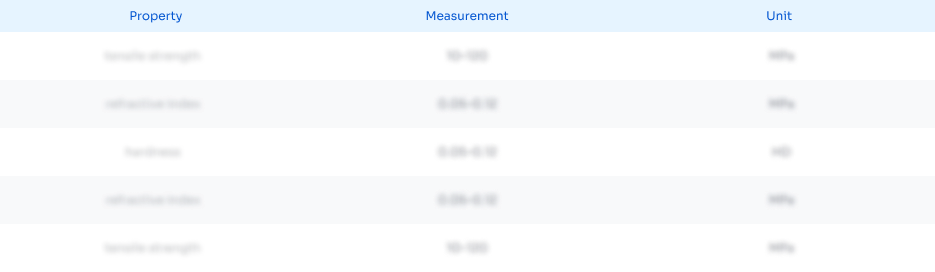
Abstract
Description
Claims
Application Information

- R&D Engineer
- R&D Manager
- IP Professional
- Industry Leading Data Capabilities
- Powerful AI technology
- Patent DNA Extraction
Browse by: Latest US Patents, China's latest patents, Technical Efficacy Thesaurus, Application Domain, Technology Topic, Popular Technical Reports.
© 2024 PatSnap. All rights reserved.Legal|Privacy policy|Modern Slavery Act Transparency Statement|Sitemap|About US| Contact US: help@patsnap.com