Electric main shaft with mouse cage type motor stator cooling structure
A motor stator and cooling structure technology, which is applied to the functional parts of the main shaft and the field of electric spindles, can solve the problem that the coaxiality between the front bearing seat hole and the motor stator is difficult to ensure, the performance parameters affecting the rotation accuracy of the electric spindle, and the difficulty of disassembling and assembling the motor stator are increased. problems, to achieve the effects of compensating axial elastic thermal deformation, facilitating processing, and simplifying the cooling structure
- Summary
- Abstract
- Description
- Claims
- Application Information
AI Technical Summary
Problems solved by technology
Method used
Image
Examples
Embodiment Construction
[0022] Figure 1 to Figure 4 It shows an embodiment of an electric spindle with a squirrel-cage motor stator cooling structure of the present invention, the electric spindle includes a spindle assembly 1, a motor stator 2, a motor rotor 3, a casing 4, a front bearing assembly 5 and a rear bearing Assembly 6, the motor stator 2 is set in the box body 4, the motor rotor 3 is set on the main shaft assembly 1, the main shaft assembly 1 is placed in the motor stator 2, and is supported by the front bearing assembly 5 and the rear bearing assembly 6 On the box body 4, a squirrel-cage cooling channel for cooling the motor stator 2 is provided on the box body 4. The front end of the box body 4 is provided with a front bearing seat 41 for installing the front bearing assembly 5, and the front bearing seat 41 and the box body 4 Casting as one body, which not only saves the sealing water jacket, reduces the radial dimension of the electric spindle, but also facilitates the coaxiality of ...
PUM
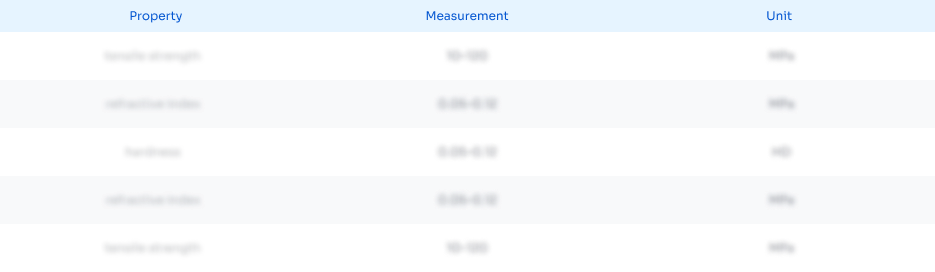
Abstract
Description
Claims
Application Information

- R&D
- Intellectual Property
- Life Sciences
- Materials
- Tech Scout
- Unparalleled Data Quality
- Higher Quality Content
- 60% Fewer Hallucinations
Browse by: Latest US Patents, China's latest patents, Technical Efficacy Thesaurus, Application Domain, Technology Topic, Popular Technical Reports.
© 2025 PatSnap. All rights reserved.Legal|Privacy policy|Modern Slavery Act Transparency Statement|Sitemap|About US| Contact US: help@patsnap.com