On-line coordination control method for plate shape and plate thickness of strip tandem hot continuous rolling mill
A technology of coordinated control and hot continuous rolling, applied in the direction of rolling mill control device, rolling force/roll gap control, metal rolling, etc., can solve complex problems, heavy burden on enterprises, high construction and operation costs, etc., and achieve simple control method , the effect of low cost control
- Summary
- Abstract
- Description
- Claims
- Application Information
AI Technical Summary
Problems solved by technology
Method used
Image
Examples
Embodiment Construction
[0034] In order to explain the specific implementation method of the patent of the present invention, taking a 6-stand hot strip rolling mill in a domestic factory as an example, the method of on-line coordinated control of plate shape and thickness is described according to the above steps for the special steel types and specifications to be rolled. .
[0035] (1) Collect the relevant equipment parameters of the hot continuous rolling mill, including the diameter D of the work rolls of each stand 1i , support roll diameter D 2i , Support roller journal diameter d 2i , roll body length L i , Depress the screw center distance l i And the stiffness M of the rolling mill (i-number of stands, i=1, 2,..., 6);
[0036] (2) Collect the relevant parameters of the original rolling specification of the rolling specifications, including the entrance and exit thickness H of each stand i 、h i , each frame reduction Δh i , the width b of the rolled piece, the plasticity coefficient Q...
PUM
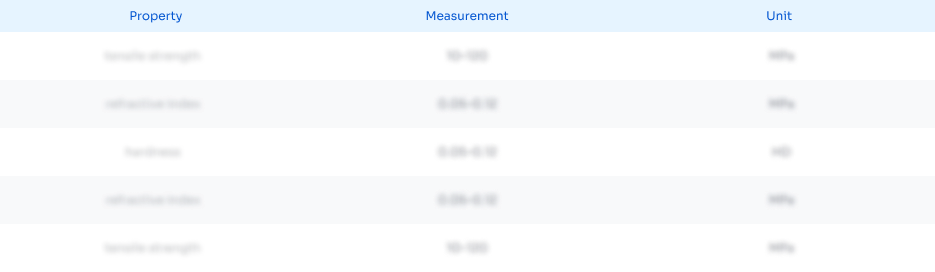
Abstract
Description
Claims
Application Information

- Generate Ideas
- Intellectual Property
- Life Sciences
- Materials
- Tech Scout
- Unparalleled Data Quality
- Higher Quality Content
- 60% Fewer Hallucinations
Browse by: Latest US Patents, China's latest patents, Technical Efficacy Thesaurus, Application Domain, Technology Topic, Popular Technical Reports.
© 2025 PatSnap. All rights reserved.Legal|Privacy policy|Modern Slavery Act Transparency Statement|Sitemap|About US| Contact US: help@patsnap.com