Positive and negative stiffness parallel three-translation vibration and impact isolation platform
A positive and negative stiffness, isolation platform technology, applied in the direction of non-rotational vibration suppression, etc., can solve the problems of not being able to bear the impact load, not being able to realize low-frequency vibration isolation, and the location and quantity of damping elements are not conducive to damping adjustment and control.
- Summary
- Abstract
- Description
- Claims
- Application Information
AI Technical Summary
Problems solved by technology
Method used
Image
Examples
Embodiment approach 1
[0019]Embodiment 1: The three-translational vibration and shock isolation platform based on positive and negative stiffness parallel connection and controllable damping includes an upper platform 1, a lower platform 9, 8 elastic branch chain structures and a silicone magnetorheological damper 11; the elastic branch chain The structure includes an upper connecting bracket 3, a guide rod 4, a positive and negative stiffness parallel uniaxial vibration isolation device 5, a lower connecting bracket 6, a radial bearing 7, and a pin shaft 8. The positive and negative stiffness parallel uniaxial vibration isolation device 5 The upper connecting bracket 3 is connected by the guide rod 4, the lower connecting bracket 6 is connected by the pin shaft 8 and the radial bearing 7, the upper connecting bracket 3 is fixed on the upper platform 1 by the bracket connecting screw 2, and the lower connecting bracket 6 is fixed by the bracket connecting screw 2 On the lower platform 9; 8 elastic b...
Embodiment approach 2
[0020] Embodiment 2: The difference between this embodiment and Embodiment 1 is that the radial bearing 7 and the guide rod linear bearing 19 adopt hydrostatic bearings to apply to large heavy-duty equipment.
PUM
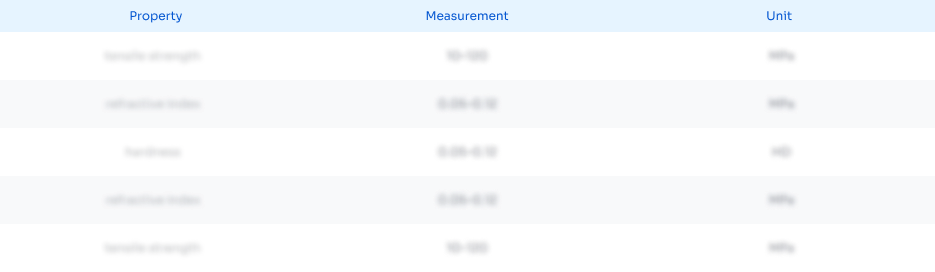
Abstract
Description
Claims
Application Information

- R&D
- Intellectual Property
- Life Sciences
- Materials
- Tech Scout
- Unparalleled Data Quality
- Higher Quality Content
- 60% Fewer Hallucinations
Browse by: Latest US Patents, China's latest patents, Technical Efficacy Thesaurus, Application Domain, Technology Topic, Popular Technical Reports.
© 2025 PatSnap. All rights reserved.Legal|Privacy policy|Modern Slavery Act Transparency Statement|Sitemap|About US| Contact US: help@patsnap.com