Spraying process of flash powder
A technology of flash powder and process, which is applied in the direction of coating, liquid coating device on the surface, surface pretreatment, etc. It can solve the problems of uneven flash powder and easy clogging of spray guns by flash powder, so as to improve surface uniformity and firmness. Not easy to fall off, the effect of saving dosage
- Summary
- Abstract
- Description
- Claims
- Application Information
AI Technical Summary
Problems solved by technology
Method used
Image
Examples
Embodiment 1
[0016] Embodiment one: flash powder spraying process, comprises the following steps successively:
[0017] A. The first spraying 1: Mix the metal baking varnish and baking varnish solvent in a ratio of 1:1 evenly, with a viscosity of 11.2 seconds, and spray it on the surface of the product;
[0018] B. Sticky flash powder 2: Roll the sprayed product in the flash powder;
[0019] C. Shake off 3: Shake the product to make the excess flash powder fall off;
[0020] D. Standing 4: Standing at room temperature for 60 minutes;
[0021] E. The second spraying 5: Mix the metal baking varnish and the baking varnish solvent at a ratio of 10:8 evenly, with a viscosity of 12.6 seconds, and spray it on the surface of the product;
[0022] F. First baking 6: Baking temperature 120°C, baking time 22 minutes;
[0023] G. The third spraying 7: Mix the metal baking varnish and the baking varnish solvent at a ratio of 10:8 evenly, with a viscosity of 12.6 seconds, and spray it on the surface ...
Embodiment 2
[0025] Embodiment two: flash powder spraying process, comprises the following steps successively:
[0026] A. The first spraying 1: Mix the metal baking varnish and baking varnish solvent in a ratio of 1:1 evenly, with a viscosity of 11.2 seconds, and spray it on the surface of the product;
[0027] B. Sticky flash powder 2: Roll the sprayed product in the flash powder;
[0028] C. Shake off 3: Shake the product to make the excess flash powder fall off;
[0029] D. Standing 4: Standing at room temperature for 75 minutes;
[0030] E. The second spraying 5: Mix the metal baking varnish and the baking varnish solvent at a ratio of 10:8 evenly, with a viscosity of 12.6 seconds, and spray it on the surface of the product;
[0031] F. The first baking 6: Baking temperature 150 ℃, baking time 20 minutes;
[0032] G. The third spraying 7: Mix the metal baking varnish and the baking varnish solvent at a ratio of 10:8 evenly, with a viscosity of 12.6 seconds, and spray it on the surf...
Embodiment 3
[0034] Embodiment three: flash powder spraying process, comprises the following steps successively:
[0035] A. The first spraying 1: Mix the metal baking varnish and baking varnish solvent in a ratio of 1:1 evenly, with a viscosity of 11.2 seconds, and spray it on the surface of the product;
[0036] B. Sticky flash powder 2: Roll the sprayed product in the flash powder;
[0037] C. Shake off 3: Shake the product to make the excess flash powder fall off;
[0038] D. Standing 4: Standing at room temperature for 90 minutes;
[0039] E. The second spraying 5: Mix the metal baking varnish and the baking varnish solvent at a ratio of 10:8 evenly, with a viscosity of 12.6 seconds, and spray it on the surface of the product;
[0040] F. First baking 6: Baking temperature 180C, baking time 18 minutes;
[0041] G. The third spraying 7: Mix the metal baking varnish and the baking varnish solvent at a ratio of 10:8 evenly, with a viscosity of 12.6 seconds, and spray it on the surface...
PUM
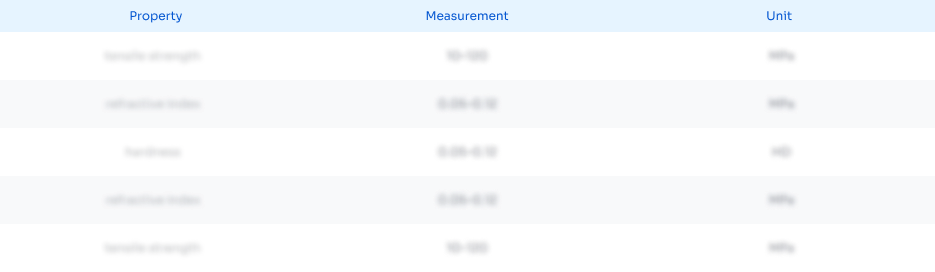
Abstract
Description
Claims
Application Information

- R&D Engineer
- R&D Manager
- IP Professional
- Industry Leading Data Capabilities
- Powerful AI technology
- Patent DNA Extraction
Browse by: Latest US Patents, China's latest patents, Technical Efficacy Thesaurus, Application Domain, Technology Topic, Popular Technical Reports.
© 2024 PatSnap. All rights reserved.Legal|Privacy policy|Modern Slavery Act Transparency Statement|Sitemap|About US| Contact US: help@patsnap.com