Blended frother for producing low ash content clean coal through flotation
A foaming agent and foam flotation technology, applied in flotation, solid separation, etc., can solve the problems of not being able to produce low clean coal, difficult to clean coal with ash content, not all coarse particles and ultrafine particles are effective, etc.
- Summary
- Abstract
- Description
- Claims
- Application Information
AI Technical Summary
Problems solved by technology
Method used
Image
Examples
Embodiment
[0030] A typical semi-bituminous flotation feed coal sample with a size of less than 0.5 mm was used in this study. The nature of coal samples is difficult to float. Ash analysis according to ASTM D 3174-73 standard indicated that the sample contained 24.5% ash. Gravimetric and ash distribution analyzes by size were performed on typical flotation feed samples. The flotation feed contained a high percentage (20%) of oversize fraction, ie -1+0.5 mm, with 23.5% ash. The oversize fraction of -0.075 mm has the largest weight contribution, about 50%, in the flotation feed content. A conventional blowing agent used for comparison is methyl isobutyl carbinol (MIBC). The improved blowing agent of the present invention described above was compared to MIBC. The flotation rates for different clean coals are shown in figure 1 . The results for each frother are given as a function of the optimum frother and collector levels as a function of the experiment.
PUM
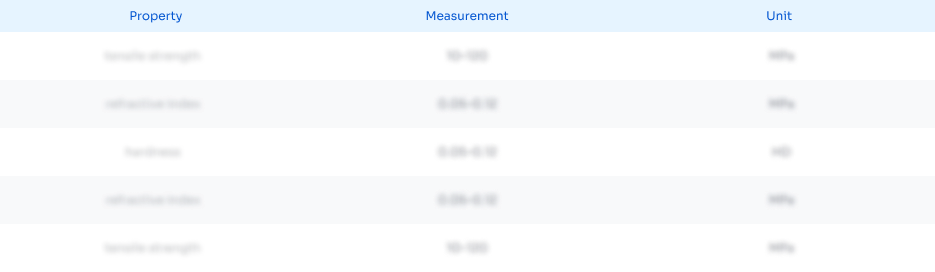
Abstract
Description
Claims
Application Information

- Generate Ideas
- Intellectual Property
- Life Sciences
- Materials
- Tech Scout
- Unparalleled Data Quality
- Higher Quality Content
- 60% Fewer Hallucinations
Browse by: Latest US Patents, China's latest patents, Technical Efficacy Thesaurus, Application Domain, Technology Topic, Popular Technical Reports.
© 2025 PatSnap. All rights reserved.Legal|Privacy policy|Modern Slavery Act Transparency Statement|Sitemap|About US| Contact US: help@patsnap.com