Redundant parallel robot system
A robot system and parallel technology, applied in the field of robot systems, can solve problems such as poor rigidity and out-of-control mechanism, and achieve the effects of simple structure, overcoming the out-of-control mechanism and improving movement speed.
- Summary
- Abstract
- Description
- Claims
- Application Information
AI Technical Summary
Problems solved by technology
Method used
Image
Examples
Embodiment Construction
[0014] The present invention will be described in detail below in conjunction with the accompanying drawings and embodiments.
[0015] Such as figure 1 , figure 2 As shown, the present invention comprises a static platform 1, and four drive motors 2 are fixedly arranged on the static platform 1, and each drive motor 2 is fixedly connected with an active rod 3, and the other end of each active rod 3 passes through a rotating pair respectively. A driven rod 4 is connected to form a branch chain, and the other end of each driven rod 4 is fixedly connected to a sensor 5 by screws, and each sensor 5 is connected to a moving platform 6 through a rotating pair. The four driving motors 2 and the four sensors 5 are electrically connected to the same controller (not shown in the figure). Each drive motor 2 has two modes of position control and force control, and can output its own position signal, angle signal and torque signal to the controller, so as to control the angular displace...
PUM
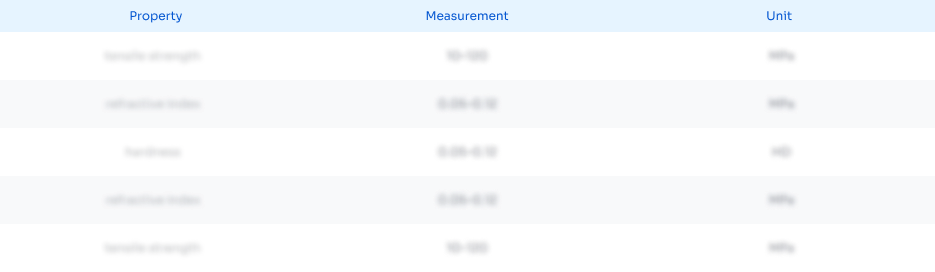
Abstract
Description
Claims
Application Information

- R&D
- Intellectual Property
- Life Sciences
- Materials
- Tech Scout
- Unparalleled Data Quality
- Higher Quality Content
- 60% Fewer Hallucinations
Browse by: Latest US Patents, China's latest patents, Technical Efficacy Thesaurus, Application Domain, Technology Topic, Popular Technical Reports.
© 2025 PatSnap. All rights reserved.Legal|Privacy policy|Modern Slavery Act Transparency Statement|Sitemap|About US| Contact US: help@patsnap.com