Magnetic pump
A magnetic pump and pump body technology, applied in the direction of pumps, pump devices, pump components, etc., can solve the problems of reducing the ability of magnetic pump to transmit torque, speed ratio, and high cost, so as to improve the ability to transmit torque, realize The effect of rotating speed ratio and improving service life
- Summary
- Abstract
- Description
- Claims
- Application Information
AI Technical Summary
Problems solved by technology
Method used
Image
Examples
Embodiment Construction
[0039] In order to have a clearer understanding of the technical features, purposes and effects of the present invention, the specific implementation manners of the present invention will now be described with reference to the accompanying drawings. Wherein, the same parts adopt the same reference numerals.
[0040] figure 1Shown is a schematic sectional view of a magnetic pump 1 according to the invention, wherein the magnetic pump 1 has a contactless magnetic gear 5 and a pump body 16 . The magnetic gears (magnetic gears) 5 shown in the figure are of disc type, of course, those skilled in the art should understand that this embodiment is only for illustration, and the magnetic gears 5 may also be of sleeve type.
[0041] The magnetic gear 5 is an independent standard structural part, which includes a housing 2, in which a driving rotor 6, a driven rotor 10, a magnetic modulating part 8, a non-conducting Magnetic isolation sleeve 11 and a bearing seat 13. The driving rotor...
PUM
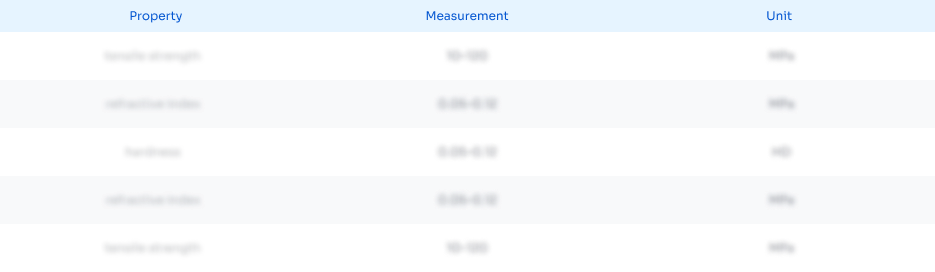
Abstract
Description
Claims
Application Information

- Generate Ideas
- Intellectual Property
- Life Sciences
- Materials
- Tech Scout
- Unparalleled Data Quality
- Higher Quality Content
- 60% Fewer Hallucinations
Browse by: Latest US Patents, China's latest patents, Technical Efficacy Thesaurus, Application Domain, Technology Topic, Popular Technical Reports.
© 2025 PatSnap. All rights reserved.Legal|Privacy policy|Modern Slavery Act Transparency Statement|Sitemap|About US| Contact US: help@patsnap.com