Spiral transmission positioning device
A positioning device, screw drive technology, applied in the direction of transmission, belt/chain/gear, mechanical equipment, etc., can solve problems such as restriction, locking, and inability to work
- Summary
- Abstract
- Description
- Claims
- Application Information
AI Technical Summary
Problems solved by technology
Method used
Image
Examples
Embodiment Construction
[0015] Such as Figure 1-3 As shown, a screw drive positioning device includes: a screw rod 10, a drive nut 20, a linear reciprocating mechanism 30 fixed together with the drive nut 20, the drive nut 20 is threaded on the screw rod 10 and the drive nut 20 is radially Fixed, at the left and right ends of the screw rod 10, a left limit stop 40 and a right limit stop 50 are respectively fixed;
[0016] One end of the screw 10 is fixedly connected to the output end of the motor 60, and the control circuit that provides the motor 60 pulse current to control the intermittent or continuous forward and reverse rotation of the motor is connected to the motor 60 according to the set time; the left and right sides of the drive nut 20 are respectively A left positioning protrusion 21 and a right positioning protrusion 22 are provided; the left limit stopper 40 is provided with a rotating protrusion 41 deviated from the axis of the screw rod 10, and the left rotating protrusion 41 and the ...
PUM
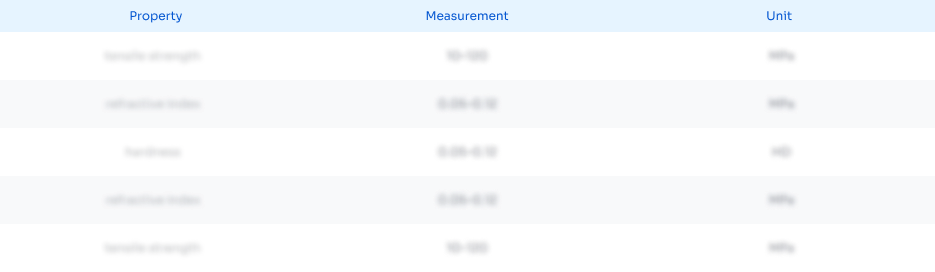
Abstract
Description
Claims
Application Information

- R&D Engineer
- R&D Manager
- IP Professional
- Industry Leading Data Capabilities
- Powerful AI technology
- Patent DNA Extraction
Browse by: Latest US Patents, China's latest patents, Technical Efficacy Thesaurus, Application Domain, Technology Topic, Popular Technical Reports.
© 2024 PatSnap. All rights reserved.Legal|Privacy policy|Modern Slavery Act Transparency Statement|Sitemap|About US| Contact US: help@patsnap.com