Thimble structure for die-casting mould
A die-casting mold and thimble technology, which is applied in the field of thimble structure for die-casting molds, can solve problems such as difficult parts removal, and achieve the effect of improving production efficiency and simple demoulding operation
- Summary
- Abstract
- Description
- Claims
- Application Information
AI Technical Summary
Problems solved by technology
Method used
Image
Examples
Embodiment Construction
[0022] Referring to Fig. 2-6, the present invention provides a thimble structure for a die-casting mold. As shown in the figure: the die-casting mold is composed of a fixed mold 1 and a movable mold 2, and the movable mold 2 is provided with a thimble 3 that can extend to the cavity for ejection. As shown in FIG. 2 , the end of the thimble 3 near the cavity of the movable mold 2 has a barb-shaped oblique notch 31 .
[0023] As a preferred embodiment, the thimbles 3 are multiple and arranged in parallel, and the barb-shaped oblique notches 31 of the thimbles have the same direction. Of course, if the direction of the barb-shaped oblique notch 31 is slightly different, the effect may be slightly worse in the demoulding operation, but it can also be implemented.
[0024] Part demoulding operation process of the present invention is as follows:
[0025] As shown in FIG. 3 , when the molten aluminum enters the cavity, the cavity and the barb-shaped oblique gap 31 of the thimble 3...
PUM
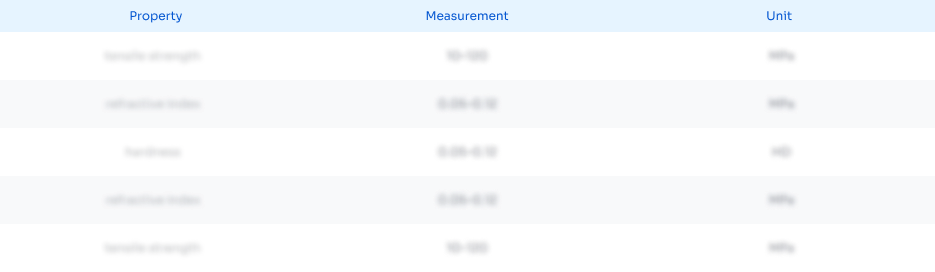
Abstract
Description
Claims
Application Information

- R&D
- Intellectual Property
- Life Sciences
- Materials
- Tech Scout
- Unparalleled Data Quality
- Higher Quality Content
- 60% Fewer Hallucinations
Browse by: Latest US Patents, China's latest patents, Technical Efficacy Thesaurus, Application Domain, Technology Topic, Popular Technical Reports.
© 2025 PatSnap. All rights reserved.Legal|Privacy policy|Modern Slavery Act Transparency Statement|Sitemap|About US| Contact US: help@patsnap.com