Transversal magnetic flux variable-reluctance permanent magnet motor
A technology of permanent magnet motor and transverse flux, applied in the direction of electrical components, electromechanical devices, electric components, etc., can solve the problems of complex secondary structure, reliability and low accuracy of current control, and achieve high accuracy of current control and light weight , the effect of improving efficiency
- Summary
- Abstract
- Description
- Claims
- Application Information
AI Technical Summary
Problems solved by technology
Method used
Image
Examples
specific Embodiment approach 1
[0009] Embodiment 1: Combining Figure 1 to Figure 27 Illustrating this embodiment, this embodiment is composed of a primary and a secondary, with an air gap between the primary and the secondary; the secondary 6 includes a secondary core 61; the primary is composed of at least one phase unit 1; each phase unit 1 is composed of a phase The unit iron core 2, the phase unit winding 3 and the permanent magnet 4 are composed; the phase unit iron core 2 is composed of several iron core units 5 to form a phase unit iron core with a tooth hole 71, and the tooth hole 71 is composed of several iron core units 5 The tooth slots 72 are alternately superimposed, the permanent magnets 4 are arranged on the teeth of the iron core unit 5, and the magnetic fields generated by the permanent magnets 4 located on the teeth of the adjacent iron core units 5 have opposite directions; the coil 31 passes through the phase unit The tooth holes 71 of the iron core 2 are wound into a phase-phase unit w...
specific Embodiment approach 2
[0010] Specific implementation mode 2: Combining figure 1 , Figure 4 , Image 6 , Figure 9 , Figure 12 , Figure 14 , Figure 15 , Figure 18 , Figure 19 and Figure 22 to Figure 27 Describing this embodiment, the difference between this embodiment and the specific embodiment 1 lies in that each tooth end of the iron core unit 5 is provided with a permanent magnet 4 . Other compositions and connection methods are the same as those in the first embodiment. The permanent magnet 4 is fixed on the tooth end by sticking, and the permanent magnet 4 is stuck on the tooth surface of the iron core unit 5 facing the air gap.
specific Embodiment approach 3
[0011] Specific implementation three: combination figure 2 , Figure 5 , Figure 10 and Figure 13 Describing this embodiment, the difference between this embodiment and the specific embodiment 1 lies in that a permanent magnet 4 is disposed between the teeth of every two adjacent iron core units in the iron core unit 5 . Other compositions and connection methods are the same as those in the first embodiment.
PUM
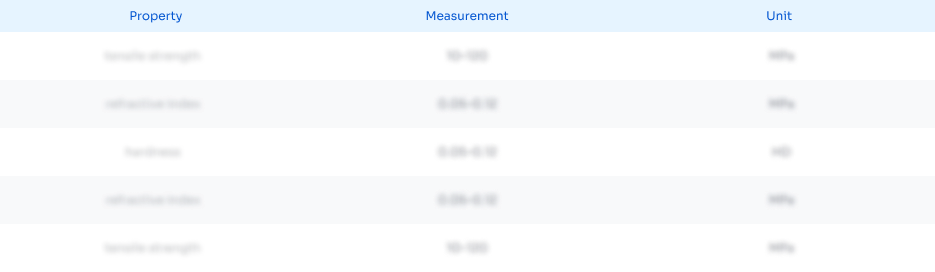
Abstract
Description
Claims
Application Information

- R&D
- Intellectual Property
- Life Sciences
- Materials
- Tech Scout
- Unparalleled Data Quality
- Higher Quality Content
- 60% Fewer Hallucinations
Browse by: Latest US Patents, China's latest patents, Technical Efficacy Thesaurus, Application Domain, Technology Topic, Popular Technical Reports.
© 2025 PatSnap. All rights reserved.Legal|Privacy policy|Modern Slavery Act Transparency Statement|Sitemap|About US| Contact US: help@patsnap.com