Fog and black surface treatment agent applying to synthetic leather rear section and preparation method thereof
A surface treatment agent, a technology for synthetic leather, applied in the direction of fiber treatment, fiber type, textiles and papermaking, etc., can solve the problems of high fog and high black effect, etc.
- Summary
- Abstract
- Description
- Claims
- Application Information
AI Technical Summary
Problems solved by technology
Method used
Image
Examples
Embodiment 1
[0025] High-speed dispersing machine production:
[0026] Add 69KG of dimethylformamide (DMF) solution, 1.0KG of low degree of polymerization fatty alcohol polyoxyethylene ether emulsifier, 3.0KG of triethanolamine, and 15.0KG of polyurethane resin, and stir evenly to form a pre-dispersion solvent.
[0027] Add 2.0KG of matting powder TS-100 under stirring. When adding matting powder, due to the low density of matting powder, the powder is easy to float. Therefore, it needs to be added very slowly. The speed of adding matting powder is 100 g / min. The stirring speed is 500 rpm, so that the pre-dispersion liquid can bring all the added matting powder into the dispersion liquid, so as to ensure the cleanness of the production environment and the accuracy of the formula. After adding all the matting powder, stir for 30 minutes at 1500 rpm to ensure complete dispersion of the matting powder.
[0028] Add 10KG of nigrosine pigment (PB1) under stirring, the nigrosine addition speed ...
Embodiment 2
[0030] High-speed dispersing machine production:
[0031] Add 48.5KG of dimethylformamide (DMF) solution, 1.5KG of low degree of polymerization fatty alcohol polyoxyethylene ether emulsifier, 6KG of triethanolamine, and 25KG of polyurethane resin, and stir evenly to form a pre-dispersion solvent.
[0032] Add 4.0KG matting powder TS-100 under stirring. When adding matting powder, due to the low density of matting powder, the powder is easy to float. Therefore, it needs to be added very slowly. The speed of adding matting powder is 100 g / min. The stirring speed is 500 rpm, so that the pre-dispersion liquid can bring all the added matting powder into the dispersion liquid, so as to ensure the cleanness of the production environment and the accuracy of the formula. After adding all the matting powder, stir for 30 minutes at 1500 rpm to ensure complete dispersion of the matting powder.
[0033] Add 15KG of nigrosine pigment (PB1) under stirring, the adding speed of nigrosine is 3...
Embodiment 3
[0035] High-speed dispersing machine production:
[0036] Add 26KG of dimethylformamide (DMF) solution, 2.0KG of low degree of polymerization fatty alcohol polyoxyethylene ether emulsifier, 9.0KG of triethanolamine, and 35.0KG of polyurethane resin, and stir evenly to form a pre-dispersion solvent.
[0037] Add 8.0KG matting powder TS-100 under stirring. When adding matting powder, due to the low density of matting powder, the powder is easy to float. Therefore, it needs to be added very slowly. The speed of adding matting powder is 100 g / min. The stirring speed is 500 rpm, so that the pre-dispersion liquid can bring all the added matting powder into the dispersion liquid, so as to ensure the cleanness of the production environment and the accuracy of the formula. After adding all the matting powder, stir for 30 minutes at 1500 rpm to ensure complete dispersion of the matting powder.
[0038] Add 20KG of nigrosine pigment (PB1) under stirring, the adding speed of nigrosine is...
PUM
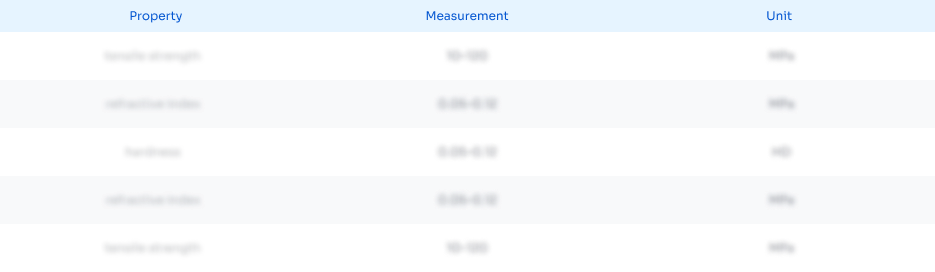
Abstract
Description
Claims
Application Information

- R&D Engineer
- R&D Manager
- IP Professional
- Industry Leading Data Capabilities
- Powerful AI technology
- Patent DNA Extraction
Browse by: Latest US Patents, China's latest patents, Technical Efficacy Thesaurus, Application Domain, Technology Topic, Popular Technical Reports.
© 2024 PatSnap. All rights reserved.Legal|Privacy policy|Modern Slavery Act Transparency Statement|Sitemap|About US| Contact US: help@patsnap.com