Exhaust system structure of film forming apparatus, film forming apparatus and method of disposing of exhaust gas
A film-forming device and gas-exhausting technology, which is applied in the fields of greenhouse gas capture, electrical components, and electrical solid devices, can solve troublesome problems and achieve the effect of reducing maintenance man-hours and costs
- Summary
- Abstract
- Description
- Claims
- Application Information
AI Technical Summary
Problems solved by technology
Method used
Image
Examples
no. 1 Embodiment approach
[0024] figure 1 It is a schematic diagram showing a film forming apparatus having an exhaust system structure according to the first embodiment of the present invention. The film forming apparatus 100 is roughly divided into a film forming processing unit 200 and an exhaust system 300 .
[0025] The film formation processing unit 200 has a substantially cylindrical processing chamber 11 . A mounting table 12 for horizontally mounting a wafer W as a substrate to be processed is disposed on the inner bottom of the processing chamber 11 . A heater 14 is embedded in the stage 12, and the heater 14 heats the wafer W serving as a substrate to be processed to a predetermined temperature. An exhaust port 16 is provided on the bottom surface of the processing chamber 11 . In addition, a wafer loading and unloading port is provided on the side wall of the processing chamber 11 and can be opened and closed by a gate valve (not shown).
[0026] A shower head 20 serving as a gas introd...
no. 2 Embodiment approach
[0051] figure 2 It is a schematic diagram showing a film forming apparatus having an exhaust system configuration according to a second embodiment of the present invention. In this second embodiment, the arrangement position of the vacuum pump 54 is different from that of the first embodiment, and is located in the H 2 Between the supply position of O and the catch mechanism 53. Therefore, when H is supplied from the oxidant supply unit 57 to the exhaust pipe 51 through the pipe 56 2 After O, it reaches the trapping mechanism 53 after passing through the vacuum pump 54, so the exhaust gas and the H as the oxidant 2 O is fully mixed in the vacuum pump 54 and recovered by the trapping mechanism 53 after complete reaction. In this regard, in the first embodiment described above, H 2 The pressure of the supply position of O to the exhaust pipe 51 is low, and the exhaust gas is mixed with H in the exhaust pipe 51 2 O is captured by the capture mechanism 53 immediately after m...
PUM
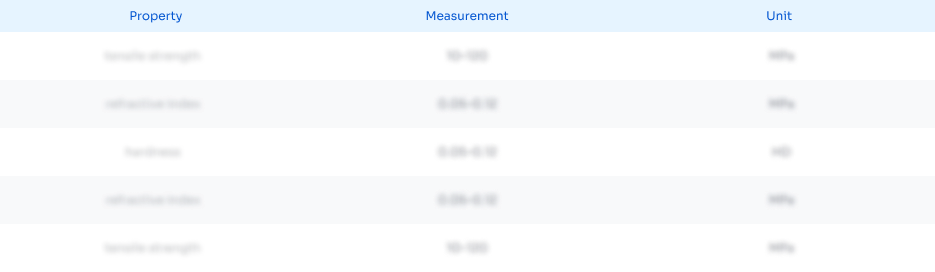
Abstract
Description
Claims
Application Information

- R&D Engineer
- R&D Manager
- IP Professional
- Industry Leading Data Capabilities
- Powerful AI technology
- Patent DNA Extraction
Browse by: Latest US Patents, China's latest patents, Technical Efficacy Thesaurus, Application Domain, Technology Topic, Popular Technical Reports.
© 2024 PatSnap. All rights reserved.Legal|Privacy policy|Modern Slavery Act Transparency Statement|Sitemap|About US| Contact US: help@patsnap.com