Large disc knitting machine support auxiliary components and manufacturing process
A technology for auxiliary components and knitting machines, which is applied in knitting, weft knitting, textiles and paper making, etc., can solve the problems of high processing cost, scratches, and heavy steel weight, so as to reduce processing costs, improve production efficiency, and reduce costs. effect of fee
- Summary
- Abstract
- Description
- Claims
- Application Information
AI Technical Summary
Problems solved by technology
Method used
Image
Examples
Embodiment 1
[0035] Embodiment 1: structure such as figure 1 As shown, a large disc knitting machine supporting auxiliary assembly includes main legs and auxiliary legs and a protective net 1 arranged on adjacent legs, a protective shell 2 is provided on the outside of each leg, and the protective net between the two legs is made of The plastic is formed by one-time injection molding, and each protective shell is formed by one-time injection molding of plastic, and the protective net 1 is connected with the protective shells 2 on both sides to form a supporting and protective ring-shaped component of the knitting machine. Above the support of the utility model are three upper plate legs 4, above-mentioned three legs are provided with a top cover 5, and the top cover 5 is formed by plastic at one time, and then assembled with the above-mentioned components as a whole, so as to achieve the purpose of easy assembly.
[0036] like figure 2 , Both sides of the protective net 1 are respectivel...
Embodiment 2
[0044] Embodiment 2: see figure 1 and image 3 , as an improvement, the entire auxiliary support assembly is divided into three groups, each consisting of a protective net 1 and a protective shell 2, the protective net 1 and the protective shell 2 on one side are injection molded at one time, and the other side of the protective net is provided with a connecting piece Connect with another set of protective shells. Others are the same as in Embodiment 1, and will not be repeated.
[0045] The plastics used in the protective net, the leg protection shell and the motor shell of the components of the present invention are elastomer environmental protection plastic materials, which can be re-formulated according to product requirements. The present invention uses a polyurethane elastomer composite material. The specific manufacturing process is as follows:
[0046] Resin mold manufacturing: 1. Coat the surface of the product with a layer of wax, and make upper and lower molds (1:...
PUM
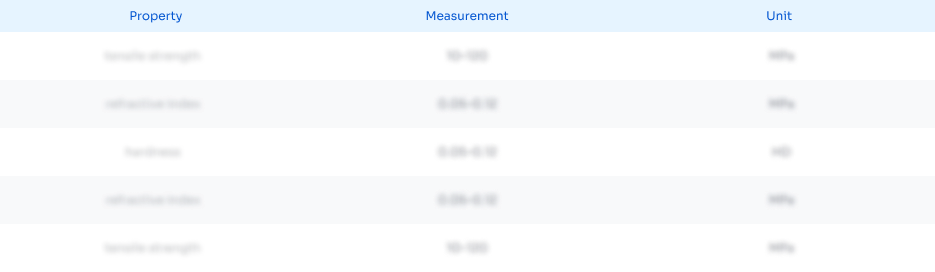
Abstract
Description
Claims
Application Information

- R&D
- Intellectual Property
- Life Sciences
- Materials
- Tech Scout
- Unparalleled Data Quality
- Higher Quality Content
- 60% Fewer Hallucinations
Browse by: Latest US Patents, China's latest patents, Technical Efficacy Thesaurus, Application Domain, Technology Topic, Popular Technical Reports.
© 2025 PatSnap. All rights reserved.Legal|Privacy policy|Modern Slavery Act Transparency Statement|Sitemap|About US| Contact US: help@patsnap.com