Polyphenylene ether resin composition and production method thereof
A technology of polyphenylene ether resin and polystyrene resin, which is applied in the field of polyphenylene ether resin composition, can solve the problems of ineffective effect and achieve small color change, which is beneficial to repeated use and improves the effect of color change
- Summary
- Abstract
- Description
- Claims
- Application Information
AI Technical Summary
Problems solved by technology
Method used
Image
Examples
Embodiment 1
[0024] 70 parts of polyphenylene ether resin (PPE) and 0.5 parts of 9,10-dihydro-9-oxa-10-phosphaphenanthrene-10-oxide (DOPO) are mixed and added from the first weight loss feeder , 30 parts of high-impact polystyrene resin (HIPS) is added from the second loss-in-weight feeder, plasticized, melted, extruded, drawn, cooled, pelletized, extruded and injected through a twin-screw extruder The temperature is between 250-320°C. The pellets were dried at 110°C for 2 h in a blast drying oven, and then test specimens were prepared by injection molding machine. At the same time, part of the pellets were taken according to the previous steps to back-extrude, granulate, and dry through the twin-screws, and the test specimens were also prepared by the injection molding machine.
Embodiment 2
[0028] 70 parts of polyphenylene ether resin (PPE), 6 parts of hydrogenated styrene-butadiene-styrene (SEBS), 0.5 parts of 9,10-dihydro-9-oxa-10-phosphaphenanthrene-10-oxid After high mixing, DOPO is added from the first loss-in-weight feeder, and 30 parts of high-impact polystyrene resin (HIPS) is added from the second loss-in-weight feeder, and then the twin-screw extruder is plasticized, Melting, extrusion, drawing, cooling, pelletizing, extrusion and injection molding temperature are between 250-320 ℃. The pellets were dried at 110°C for 2 h in a blast drying oven, and then test specimens were prepared by injection molding machine. At the same time, part of the pellets were taken according to the previous steps to back-extrude, granulate, and dry through the twin-screws, and the test specimens were also prepared by the injection molding machine.
Embodiment 3
[0031] Example 3: 70 parts of polyphenylene ether resin (PPE), 8 parts of hydrogenated styrene-butadiene-styrene (SEBS), 0.5 part of 9,10-dihydro-9-oxa-10-phosphaphenanthrene -10-Oxide (DOPO) is added from the first loss-in-weight feeder after high-mixing, 30 parts of high-impact polystyrene resin (HIPS) is added from the second loss-in-weight feeder, and 8 parts of liquid flame retardant The agent is added from the liquid feed port through a liquid pump, and then the twin-screw extruder is plasticized, melted, extruded, drawn, cooled, and pelletized. The extrusion and injection molding temperatures are between 250-320°C. The pellets were dried at 110°C for 2 h in a blast drying oven, and then test specimens were prepared by injection molding machine. At the same time, part of the pellets were taken according to the previous steps to back-extrude, granulate, and dry through the twin-screws, and the test specimens were also prepared by the injection molding machine.
[0032] T...
PUM
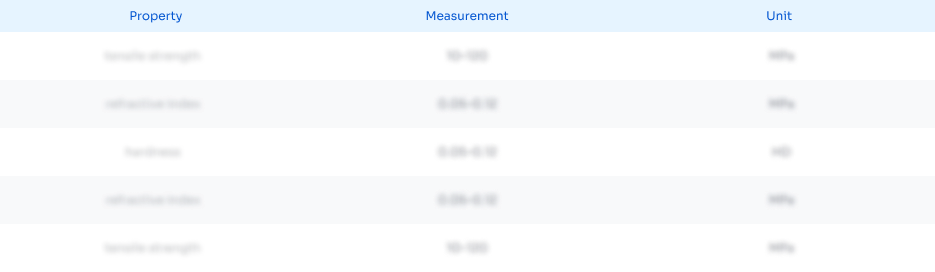
Abstract
Description
Claims
Application Information

- R&D
- Intellectual Property
- Life Sciences
- Materials
- Tech Scout
- Unparalleled Data Quality
- Higher Quality Content
- 60% Fewer Hallucinations
Browse by: Latest US Patents, China's latest patents, Technical Efficacy Thesaurus, Application Domain, Technology Topic, Popular Technical Reports.
© 2025 PatSnap. All rights reserved.Legal|Privacy policy|Modern Slavery Act Transparency Statement|Sitemap|About US| Contact US: help@patsnap.com