Shipping box, corrugated board blank sheet, and rule mark ring assembly
A crease line and packaging box technology, applied in the field of corrugated paper semi-finished board, crease line wheel assembly, and packaging box, can solve problems such as damage and appearance, and achieve the effect of suppressing the twists and turns of the crease and making it easy to form.
- Summary
- Abstract
- Description
- Claims
- Application Information
AI Technical Summary
Problems solved by technology
Method used
Image
Examples
no. 1 approach
[0064] Hereinafter, a packaging box according to one embodiment of the present invention will be described with reference to the drawings. here, figure 1 It is a corrugated semi-finished board used to form packaging boxes.
[0065] Corrugated semi-finished board
[0066] Such as figure 1 As shown, the corrugated cardboard semi-finished board 1 used in the packaging box according to this embodiment has: a top surface portion 3 that becomes the upper surface when assembled as a packaging box; first and second ribs M1 and M2 adjacent to the top surface portion 3; Connected to the first long side portion 5 of the top surface portion 3 across the second rib M2; the third rib M3 adjacent to the first long side portion 5; connected to the first long side portion 5 across the third rib M3 the bottom portion 7; and the fourth edge M4 adjacent to the bottom portion 7 after assembly. In addition, the second long side portion 9 is connected to the top surface portion 3 via the first...
no. 2 approach
[0080] Below, according to Figure 4 A second embodiment will be described. This second embodiment is different from the first embodiment in the structure of the crease line K3. That is, if Figure 4 As shown in (B), the feature of this embodiment is that it is formed by one crease line K3 having a wide width. Therefore, this crease line K3 directly becomes the edge M22. When described in more detail, the crease line K3 is formed at a portion sandwiched between the top surface portion 3 and the long side portion 5 . Furthermore, the depth of the crease line K3 becomes deeper continuously as it approaches from the top surface portion 3 side to the long side portion 5 side. As a result, the thickness of the corrugated cardboard blank at the crease line K3 gradually becomes thinner as it approaches the long side portion 5 .
[0081] By employing the above configuration, the following effects are produced. That is, since the thickness of the corrugated cardboard blank 101 is...
no. 3 approach
[0083] Below, according to Figure 5 A third embodiment will be described. Although the third embodiment is similar to the second embodiment, the cross-sectional shape of the crease line K4 is different. That is, if Figure 5 As shown in (B), the depth of the crease line K4 changes stepwise, and the long side portion 5 side is the deepest. Therefore, the thickness of the corrugated cardboard blank 201 is the thinnest on the long side part 5 side. When a bending stress is applied to such a corrugated cardboard blank 201 , the boundary portion with the long side portion 5 bends first. Therefore, there is no problem that the bend line is meandered. Furthermore, when the bending stress is gradually increased, the bending proceeds toward the top surface portion 3 side. At this time, since the thickness at the crease line K4 changes stepwise, it becomes the edge M32 in a state of being bent and deformed in a polygonal cross-sectional shape. Even when the packaging box is forme...
PUM
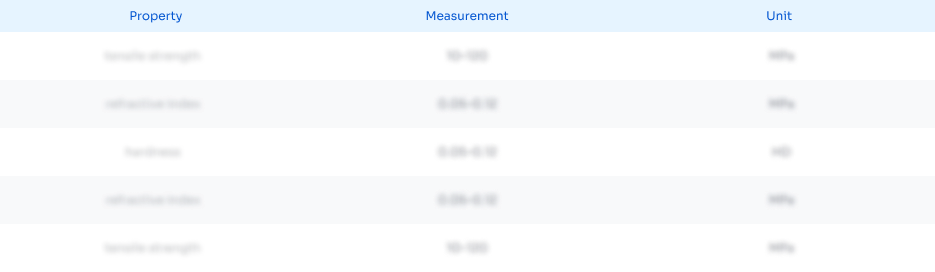
Abstract
Description
Claims
Application Information

- R&D
- Intellectual Property
- Life Sciences
- Materials
- Tech Scout
- Unparalleled Data Quality
- Higher Quality Content
- 60% Fewer Hallucinations
Browse by: Latest US Patents, China's latest patents, Technical Efficacy Thesaurus, Application Domain, Technology Topic, Popular Technical Reports.
© 2025 PatSnap. All rights reserved.Legal|Privacy policy|Modern Slavery Act Transparency Statement|Sitemap|About US| Contact US: help@patsnap.com