Cooling structure of crankcase of directly coupled type air compressor
A technology of air compressor and cooling structure, applied in the direction of liquid variable capacity machinery, mechanical equipment, variable capacity pump components, etc. problem, to achieve the effect of lowering the temperature
- Summary
- Abstract
- Description
- Claims
- Application Information
AI Technical Summary
Problems solved by technology
Method used
Image
Examples
Embodiment Construction
[0018] The present invention will be further described below with specific embodiment: see Figure 1-5 :
[0019] Direct-coupled air compressor crankcase cooling structure, which includes: cooling fan 1, housing 2, motor stator 3, motor rotor 4, crankcase 5, crankshaft 6 and cylinder 7, the motor stator 3 and crankcase 5 Tightly connected, the motor rotor 4 is supported on the bearing seat hole of the crankcase 5 through the crankshaft 6 and the main bearing 8; one end of the cylinder 7 is tightly connected with the crankcase 5, and the other end of the cylinder 7 is connected with a valve seat 9 and The cylinder head 10, wherein the valve seat 9 and the cylinder head 10 can be made in one piece; it should be pointed out that the above-mentioned housing 2 covers the motor stator 3, the crankcase 5, the cylinder 7, the valve seat 9 or the cylinder head 10 in whole or in part. In it, the so-called air passage 11 is formed, and the air passage 11 can be formed by one flow passag...
PUM
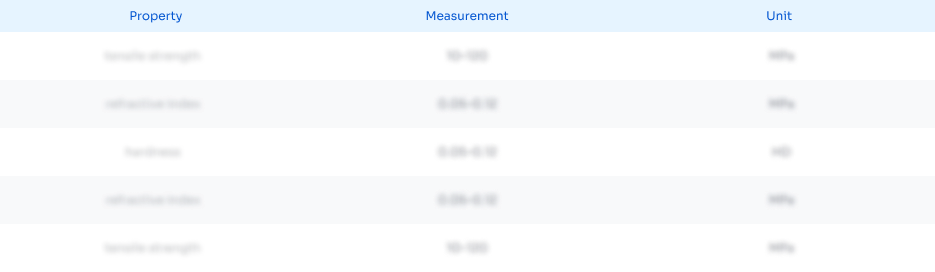
Abstract
Description
Claims
Application Information

- Generate Ideas
- Intellectual Property
- Life Sciences
- Materials
- Tech Scout
- Unparalleled Data Quality
- Higher Quality Content
- 60% Fewer Hallucinations
Browse by: Latest US Patents, China's latest patents, Technical Efficacy Thesaurus, Application Domain, Technology Topic, Popular Technical Reports.
© 2025 PatSnap. All rights reserved.Legal|Privacy policy|Modern Slavery Act Transparency Statement|Sitemap|About US| Contact US: help@patsnap.com