Preparation method of yarn with long and short fiber compound structure
A technology of fiber compounding and production method, which is applied in the directions of yarn, spinning machine, continuous winding spinning machine, etc., can solve the problems of difficulty in production, large torque, spinning failure, etc., and achieves convenient operation and simple equipment modification. row effect
- Summary
- Abstract
- Description
- Claims
- Application Information
AI Technical Summary
Problems solved by technology
Method used
Image
Examples
Embodiment 1
[0028] Embodiment 1, the composite structure yarn of cotton fiber coating polyester filament (monofilament)
[0029] On the cotton spinning ring spinning frame, the cotton fiber roving sliver a is unwound from the roving bobbin, fed into the drafting zone by the back roller 2 through the guide horn 1, and three polyester filaments (12D / 1F) b, b′, b ″ are respectively guided by the positioning guide mechanism to feed in parallel from the rear end of the front roller 5 with a spacing of 0.5mm. The polyester filaments b, b′, b″ and the cotton roving strands a are parallel to each other and converge at the front jaw 6. The three filaments b, b', b" are all located within the width boundary of the roving sliver (such as figure 2 shown), the drawn cotton roving strip a and the filaments b, b', b" are output from the front jaws and enter the twisting triangle area, and the composite yarn 8 formed after twisting passes through the yarn guide hook 7 Wound on the spun bobbin 9. The in...
Embodiment 2
[0030]Embodiment 2, make the composite yarn that polyester filament (monofilament) wraps cotton short fiber
[0031] On the cotton spinning ring spinning frame, the cotton fiber roving sliver a is unwound from the roving bobbin, fed into the drafting zone by the back roller 2 through the guide horn 1, and three polyester filaments (12D / 1F) b, b′, b "respectively guided by the positioning guide wire mechanism to feed in parallel from the rear end of the front roller 5 with a spacing of 2mm, and the polyester filaments b, b', b" and the cotton roving strands a are parallel to each other and converge at the front jaw 6. Among them, the polyester filaments b and b″ are respectively located outside the width boundary range of the roving strand a, and the polyester filament b′ is located inside the width boundary range of the roving strand a (see image 3 ), after drafting, the cotton roving strip a and filaments b, b', b" are output from the front jaws and enter the twisting triang...
Embodiment 3
[0032] Embodiment 3, making pure cotton fiber ultra-high count yarn
[0033] The long-staple cotton fiber roving strand a is unwound from the roving bobbin, fed into the drafting zone by the rear roller 2 through the guide horn 1, and three fine denier water-soluble vinylon filaments (12D / 1F) b, b', b "respectively guided by the positioning guide wire mechanism to feed in parallel with the 0.5mm spacing from the rear end of the front roller 5, and the vinylon filaments b, b', b" and the cotton roving strands a are parallel to each other and converge at the front jaw 6. The three filaments b, b', b" are located inside the width boundary of the roving strands (such as figure 2 shown), the drawn cotton roving strip a and the filaments b, b', b" are output from the front jaws and enter the twisting triangle area, and the composite yarn 8 formed after twisting passes through the yarn guide hook 7 Winding on the spun bobbin 9. The spun long and short fiber composite yarn is dissol...
PUM
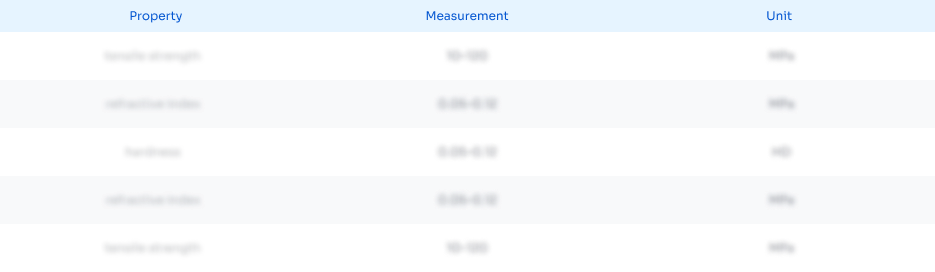
Abstract
Description
Claims
Application Information

- R&D
- Intellectual Property
- Life Sciences
- Materials
- Tech Scout
- Unparalleled Data Quality
- Higher Quality Content
- 60% Fewer Hallucinations
Browse by: Latest US Patents, China's latest patents, Technical Efficacy Thesaurus, Application Domain, Technology Topic, Popular Technical Reports.
© 2025 PatSnap. All rights reserved.Legal|Privacy policy|Modern Slavery Act Transparency Statement|Sitemap|About US| Contact US: help@patsnap.com