Casting mixture for epoxy casting transformer and preparation method thereof
A technology of epoxy casting and preparation method, which is applied in the field of epoxy casting, which can solve the problems of lower quality of casting transformer products, difficult diffusion of air bubbles, insufficient wetting of mixture, etc., to improve market competitiveness and reduce shrinkage and thermal expansion coefficient, beautify the appearance of the effect
- Summary
- Abstract
- Description
- Claims
- Application Information
AI Technical Summary
Problems solved by technology
Method used
Examples
Embodiment 1
[0017] The casting mixture of the epoxy casting transformer of the present invention includes the following raw materials in parts by weight: 1 part of epoxy resin, 2.5 parts of silicon micropowder, 0.1 part of toughening agent, 0.6 part of curing agent, and 0.001 part of accelerator. (All raw materials are commercially available products)
[0018] The pouring compound preparation method of the epoxy pouring transformer of the present invention comprises the following steps:
[0019] (1) Chemicals:
[0020] Put the epoxy resin in an oven, set the temperature at 95°C, and melt it into a dilute liquid; put the silicon micropowder in a container and place it in the oven, set the temperature at 95°C, and pre-bake for 6 hours;
[0021] (2) Preparation:
[0022] 1) First start the heating device of the mixing tank to ensure that the temperature in the tank is 95°C, add molten epoxy resin according to the above-mentioned parts by weight, then start the stirring device, and mix the ...
Embodiment 2
[0025] The casting compound of the epoxy casting transformer of the present invention includes the following raw materials in parts by weight: 1 part of epoxy resin, 2.6 parts of silicon micropowder, 0.12 parts of toughening agent, 0.01 part of color paste, 0.62 parts of curing agent, and 0.0015 parts of accelerator share. (All raw materials are commercially available products)
[0026] The pouring compound preparation method of the epoxy pouring transformer of the present invention comprises the following steps:
[0027] (1) Chemicals:
[0028] Put the epoxy resin in an oven, set the temperature at 105°C, and melt it into a dilute liquid; put the silicon micropowder in a container and place it in the oven, set the temperature at 105°C, and pre-bake for 6.5 hours;
[0029] (2) Preparation:
[0030] 1) First start the heating device of the mixing tank to ensure that the temperature in the tank is 105°C, add molten epoxy resin according to the above-mentioned parts by weight,...
Embodiment 3
[0033] The casting compound of the epoxy casting transformer of the present invention includes the following raw materials in parts by weight: 1 part of epoxy resin, 2.9 parts of silicon micropowder, 0.16 parts of toughening agent, 0.015 parts of color paste, 0.66 parts of curing agent, and 0.002 parts of accelerator. share.
[0034] The pouring compound preparation method of the epoxy pouring transformer of the present invention comprises the following steps:
[0035] (1) Chemicals:
[0036] Put the epoxy resin in an oven, set the temperature at 120°C, and melt it into a dilute liquid; put the silicon micropowder in a container and place it in the oven, set the temperature at 120°C, and pre-bake for 7 hours;
[0037] (2) Preparation:
[0038] 1) First start the heating device of the mixing tank to ensure that the temperature in the tank is 120°C, add molten epoxy resin according to the above-mentioned parts by weight, then start the stirring device, and mix the pre-baked si...
PUM
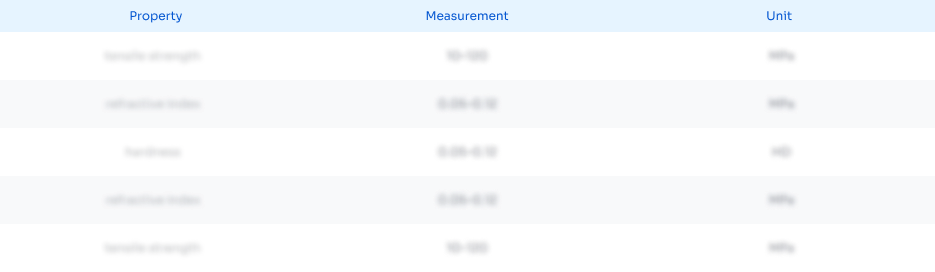
Abstract
Description
Claims
Application Information

- Generate Ideas
- Intellectual Property
- Life Sciences
- Materials
- Tech Scout
- Unparalleled Data Quality
- Higher Quality Content
- 60% Fewer Hallucinations
Browse by: Latest US Patents, China's latest patents, Technical Efficacy Thesaurus, Application Domain, Technology Topic, Popular Technical Reports.
© 2025 PatSnap. All rights reserved.Legal|Privacy policy|Modern Slavery Act Transparency Statement|Sitemap|About US| Contact US: help@patsnap.com