Method for producing phenolic resin by utilizing paraformaldehyde
A paraformaldehyde and phenolic resin technology, applied in the field of phenolic resin production, can solve the problems of inconvenient transportation of liquid formaldehyde, pollution of the environment by waste water, and large energy consumption
- Summary
- Abstract
- Description
- Claims
- Application Information
AI Technical Summary
Problems solved by technology
Method used
Examples
Embodiment 1
[0019] (1), back up raw materials according to the following weight ratio:
[0020] Phenol 350kg,
[0021] Paraformaldehyde 176kg,
[0022] Sodium hydroxide 1.5kg,
[0023] Barium hydroxide 10kg,
[0024] Urea 14kg,
[0025] 80kg of water;
[0026] (2), put the phenol, sodium hydroxide and barium hydroxide prepared in step (1) into the reaction kettle, and stop heating after the temperature in the kettle is raised to 60°C. Put 22kg of paraformaldehyde into the reaction kettle, and control the temperature in the kettle, and the temperature control range is 75-95°C. After putting paraformaldehyde into the reactor for the first time, put 22kg of paraformaldehyde into the reactor every 15 to 25 minutes, and finish 7 times;
[0027] (3) Control the temperature in the kettle in the range of 75-85°C and keep it warm for 60 minutes. Then the temperature was raised to 95-110°C for 30 minutes at high temperature. Then use the conventional method to test the emulsification point ...
Embodiment 2
[0030] (1), back up raw materials according to the following weight ratio:
[0031] Phenol 400g,
[0032] Paraformaldehyde 224g,
[0033] Sodium hydroxide 2g,
[0034] Barium hydroxide 15g,
[0035] Urea 20g,
[0036] 150g of water;
[0037] (2), put the phenol, sodium hydroxide and barium hydroxide prepared in step (1) into the reaction kettle, and stop heating after the temperature in the kettle is raised to 60°C. Put 28g of paraformaldehyde into the reaction kettle, control the temperature in the kettle, and the temperature control range is 75~95℃. After putting paraformaldehyde into the reactor for the first time, put 28g of paraformaldehyde into the reactor every 15 to 25 minutes, and finish 7 times;
[0038] (3) Control the temperature in the kettle in the range of 75-85°C and keep it warm for 80 minutes. Then the temperature was raised to 95-110°C for 50 minutes at high temperature. Then use the conventional method to test the emulsification point of the phenoli...
PUM
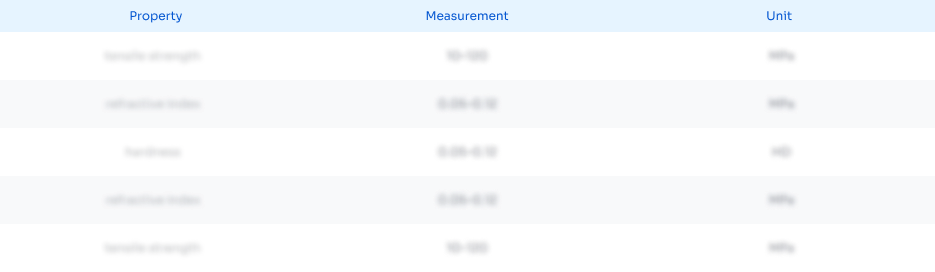
Abstract
Description
Claims
Application Information

- R&D Engineer
- R&D Manager
- IP Professional
- Industry Leading Data Capabilities
- Powerful AI technology
- Patent DNA Extraction
Browse by: Latest US Patents, China's latest patents, Technical Efficacy Thesaurus, Application Domain, Technology Topic, Popular Technical Reports.
© 2024 PatSnap. All rights reserved.Legal|Privacy policy|Modern Slavery Act Transparency Statement|Sitemap|About US| Contact US: help@patsnap.com