Method for dehydrating micro-particle slurry
A technology of fine particles and slurry, applied in separation methods, chemical instruments and methods, filtration separation, etc., can solve problems such as poor filtration performance
- Summary
- Abstract
- Description
- Claims
- Application Information
AI Technical Summary
Problems solved by technology
Method used
Image
Examples
Embodiment 1
[0024] A bauxite concentrate with a concentration of 10% is classified by an inclined plate thickening box with a stirring device. +10μm coarse grain concentrate with 82% content is increased to 65% by a high-efficiency thickener, and then filtered and dehydrated by a ceramic filter. 300mm, the slurry temperature is 22°C, and the filtration capacity is changed from the original 210kg / m 2 ·h increased to 442kg / m 2 ·h, filter cake moisture 11.2%. -10μm content of 86% fine particle concentrate is concentrated by high-efficiency thickener under the condition of pH = 5.6, and the concentration is increased to 44%. After the concentration is increased to 44%, it is filtered and dehydrated by a diaphragm filter press. The feeding pressure is 0.85MPa and the pressing pressure is . 1.5MPa, press filter for 8min, high pressure air pressure is 0.4-0.6MPa, backflush for 3min, moisture content of filter cake is 18.3%.
Embodiment 2
[0026] An iron ore concentrate with a concentration of 12% is classified by a secondary hydrocyclone. +10μm Coarse particle concentrate with 85% content is settled and concentrated by high-efficiency thickener. After the concentration is increased to 72%, it is filtered and dehydrated by microporous filter. The filtration time is 7-12min, the filtration pressure is 0.05-0.12MPa, and the drying air pressure is 0.1 -0.15MPa, the drying time is 15min, and the filtration capacity is increased from the original 300kg / m2·h to 590kg / m 2 ·h, filter cake moisture 8.6%. -10μm content of 90% fine-grain concentrate is concentrated by high-efficiency thickener sedimentation, and the concentration is increased to 48%. After the concentration is increased to 48%, it is filtered and dehydrated by a diaphragm filter press. The feeding pressure is 0.75MPa, the feeding time is 1.5min, and the pressing pressure is 1.2MPa. Press filtration for 6.5 minutes, high pressure air pressure is 0.4-0.6 MP...
Embodiment 3
[0028] A bauxite beneficiation concentrate with a concentration of 15% is classified under the action of a hydrocyclone. +10μm coarse-grain concentrate with 76% content is concentrated by high-efficiency thickener under the condition of pH=7.4. After the concentration is increased to 67%, it is filtered and dehydrated by vertical disc filter. The vacuum degree is 0.38MPa, and the filtration capacity is changed from the original 210kg / m 2 ·h increased to 480kg / m 2 ·h, filter cake moisture 11.6%. The fine-grained ore concentrate with a content of -10μm of 81% is concentrated by high-efficiency thickener under the condition of pH=5.4, and the concentration is increased to 53%. After the concentration is increased to 53%, it is filtered and dehydrated by a horizontal screw centrifugal dehydrator. The differential speed of the screw pusher is 15r / min, and the water content of the filter cake is 17.8%.
PUM
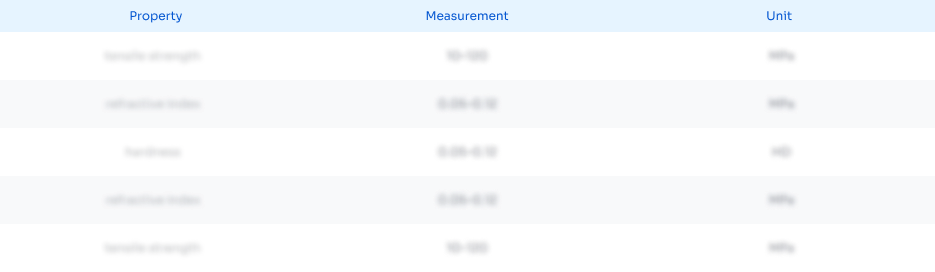
Abstract
Description
Claims
Application Information

- R&D
- Intellectual Property
- Life Sciences
- Materials
- Tech Scout
- Unparalleled Data Quality
- Higher Quality Content
- 60% Fewer Hallucinations
Browse by: Latest US Patents, China's latest patents, Technical Efficacy Thesaurus, Application Domain, Technology Topic, Popular Technical Reports.
© 2025 PatSnap. All rights reserved.Legal|Privacy policy|Modern Slavery Act Transparency Statement|Sitemap|About US| Contact US: help@patsnap.com