2-PRT and PRS spatial parallel robotic mechanism with three degrees of freedom (DOF)
- Summary
- Abstract
- Description
- Claims
- Application Information
AI Technical Summary
Problems solved by technology
Method used
Image
Examples
Embodiment 1
[0019] A spatial parallel robot mechanism with one translation and two rotations realized by using fewer kinematic pairs. The mechanism is composed of a moving platform 1, a fixed platform 2 and three branch chains M3, M4 and M5 connecting the above two platforms; the branch chains M3 and M4 are respectively composed of a Hooke hinge T1, T2 and a moving hinge P1 from top to bottom. , P2, a rotating hinge R1, R2 and connecting rods L1, L2, L3, L4 between them; branch chain M5 consists of a ball hinge S1, a moving hinge P3, a rotating hinge R3 and their Between the connecting rod L5, L6 composition. The connecting rods L2, L4, L6 and the movable hinges P1, P2, P3 of the fixed platform 2 are the driving pairs of the mechanism, and the axes of the rotating hinges R1, R2, R3 adjacent to the driving pair are respectively perpendicular to the axis of the driving pair, passing through Hooke The hinges T1, T2 and the ball hinge S1 connect the rods L1, L3, L5 to the motion platform 1, ...
PUM
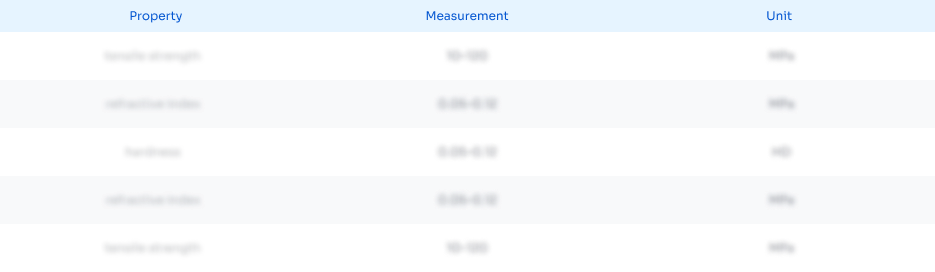
Abstract
Description
Claims
Application Information

- R&D Engineer
- R&D Manager
- IP Professional
- Industry Leading Data Capabilities
- Powerful AI technology
- Patent DNA Extraction
Browse by: Latest US Patents, China's latest patents, Technical Efficacy Thesaurus, Application Domain, Technology Topic, Popular Technical Reports.
© 2024 PatSnap. All rights reserved.Legal|Privacy policy|Modern Slavery Act Transparency Statement|Sitemap|About US| Contact US: help@patsnap.com