Manufacturing method for root part of megawatt wind turbine blade
A technology of wind turbine blades and manufacturing methods, which is applied to other household appliances, household appliances, household components, etc., can solve problems such as temperature rise, deformation, and prefabricated parts cannot be placed in the mold, and achieve the effect of eliminating collapse
- Summary
- Abstract
- Description
- Claims
- Application Information
AI Technical Summary
Problems solved by technology
Method used
Image
Examples
Embodiment Construction
[0020] A method for manufacturing the root of a megawatt wind rotor blade, which is an improvement on the traditional direct laying of hundreds of layers of glass fiber cloth, and its specific steps are as follows:
[0021] (1) Plug-in production:
[0022] First make the plug-in male mold shell 3, and make a male mold shell of an auxiliary mechanism with steel, fiber, and resin. The outer diameter of the male mold shell 3 is the inner diameter of the blade mold minus the thickness of the fiber that needs to be auxiliary laid. The size does not need to be too accurate.
[0023] A tensioning mechanism is arranged in the concave surface of the plug-in male mold housing 3, the tensioning mechanism includes a top support rod 1, a lateral support rod 4, and a rotating shaft 6 and a lifting shaft 5 arranged side by side, and the rotating shaft 6 and the lifting shaft 5 are connected as one , the two ends of the rotating shaft 6 are installed on the brackets 7 on both sides, the inner...
PUM
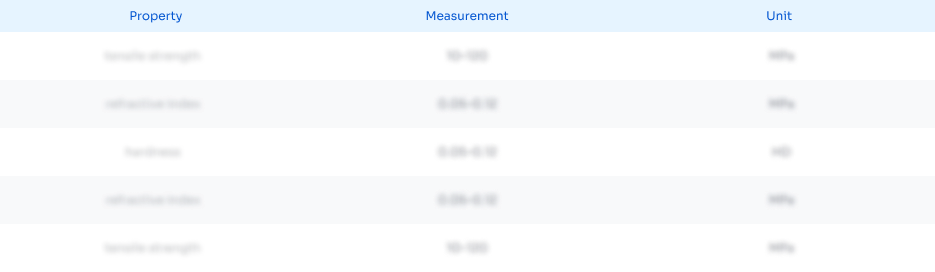
Abstract
Description
Claims
Application Information

- R&D Engineer
- R&D Manager
- IP Professional
- Industry Leading Data Capabilities
- Powerful AI technology
- Patent DNA Extraction
Browse by: Latest US Patents, China's latest patents, Technical Efficacy Thesaurus, Application Domain, Technology Topic, Popular Technical Reports.
© 2024 PatSnap. All rights reserved.Legal|Privacy policy|Modern Slavery Act Transparency Statement|Sitemap|About US| Contact US: help@patsnap.com