Strain control method of cantilever bending and loading low-circle fatigue test
A low-cycle fatigue and strain control technology, applied in the field of testing, to achieve the effects of improving test accuracy, reducing labor intensity and saving test costs
- Summary
- Abstract
- Description
- Claims
- Application Information
AI Technical Summary
Problems solved by technology
Method used
Image
Examples
Embodiment Construction
[0021] Such as Figure 4 As shown, the present invention proposes a strain control method for cantilever bending loading low-cycle fatigue test. The COD gauge clamping knife edge 8 designed on the original sample is located on one side of the sample arc, and the angles on both sides of the knife edge are 45 degrees, which is less than the 60-degree angle of the groove at the end of the two elastic arms of the COD gauge. The distance between the two elastic arms of the COD gauge 9 is about 20mm, and the distance between the knife edges is 10mm, which is the gauge length of the COD gauge. Squeeze the two elastic arms of the COD gauge firmly to make it less than 10mm, and then clamp the 60-degree grooves at the ends of the two elastic arms of the COD gauge between the 45-degree knife-edge grooves. With the self-elasticity of the two elastic arms, the COD The gauge is fixed on the edge of the knife.
[0022] According to the principle of the one-to-one correspondence relationship...
PUM
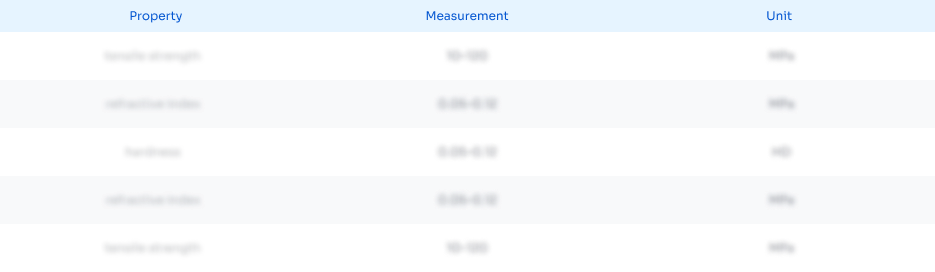
Abstract
Description
Claims
Application Information

- R&D
- Intellectual Property
- Life Sciences
- Materials
- Tech Scout
- Unparalleled Data Quality
- Higher Quality Content
- 60% Fewer Hallucinations
Browse by: Latest US Patents, China's latest patents, Technical Efficacy Thesaurus, Application Domain, Technology Topic, Popular Technical Reports.
© 2025 PatSnap. All rights reserved.Legal|Privacy policy|Modern Slavery Act Transparency Statement|Sitemap|About US| Contact US: help@patsnap.com