Pressing load distribution method for double-stander medium plate production line
A load distribution, double-stand technology, applied in rolling mill control devices, metal processing equipment, metal rolling, etc., can solve problems such as inability to adopt tandem rolling process, inability to apply actual production, and inability to realize continuous rolling process.
- Summary
- Abstract
- Description
- Claims
- Application Information
AI Technical Summary
Problems solved by technology
Method used
Image
Examples
Embodiment Construction
[0057] The present invention will be further described below in combination with specific embodiments.
[0058] Taking the production line of a two-stand four-high rolling mill as an example, the material of the steel plate is Q235, the thickness of the slab is 220 mm, the width of the slab is 1500 mm, the length of the slab is 1000 mm, the thickness of the finished product is 12 mm, and the slab inlet temperature of the first rolling mill is 1150 °C.
[0059] Step 1. Obtain the incoming thickness H of the steel plate 1 =220mm and finished product thickness H 2 =12mm
[0060] Step 2. Determine the optional range of intermediate billets between the two rolling mills
[0061] In step one, the incoming thickness H of the steel plate is known 1 And finished product thickness H 2 Under the premise of , determine the optional range of intermediate blanks based on experience, h 1 =80mm, h 2 =25mm, represented by (80,25), satisfying H 1 >h 1 >h 2 >H 2 .
[0062] Step 3. Use...
PUM
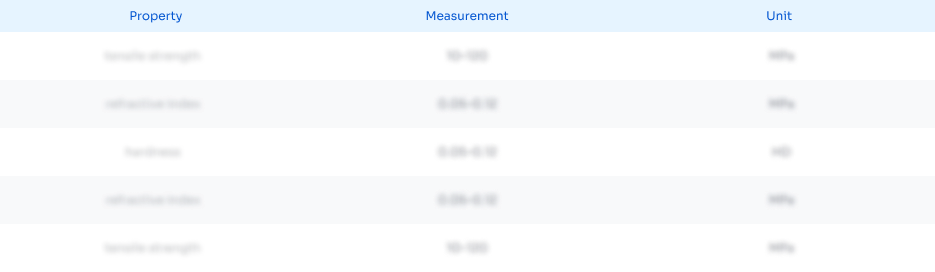
Abstract
Description
Claims
Application Information

- R&D Engineer
- R&D Manager
- IP Professional
- Industry Leading Data Capabilities
- Powerful AI technology
- Patent DNA Extraction
Browse by: Latest US Patents, China's latest patents, Technical Efficacy Thesaurus, Application Domain, Technology Topic, Popular Technical Reports.
© 2024 PatSnap. All rights reserved.Legal|Privacy policy|Modern Slavery Act Transparency Statement|Sitemap|About US| Contact US: help@patsnap.com