Passive force/moment feedback driver of man-machine interface device for controlling remote-control operation robot
A technology for teleoperating robots and human-machine interfaces, applied in the field of passive force/torque feedback drives, can solve the problems of discontinuous driving torque, stick-slip, high dynamic friction coefficient, etc., and achieve the effect of large torque, simple device structure and small size
- Summary
- Abstract
- Description
- Claims
- Application Information
AI Technical Summary
Problems solved by technology
Method used
Image
Examples
Embodiment Construction
[0020] Below in conjunction with accompanying drawing, the present invention is described in detail:
[0021] A passive force / torque feedback driver for a man-machine interface device controlled by a teleoperated robot, comprising a base 15 and an upper cover 2, threaded holes are set on the outer circumference of the base 15 and the upper cover 2, and bolts 1 are used to secure the The base 15 is fixed to the upper cover 2, and a torque feedback shaft 5 is arranged between the base 15 and the upper cover 2. The torque feedback shaft 5 is provided with a moving friction plate 11 and a moving gasket 14, and the moving friction plate 11 is separated by the moving gasket 14. Positioning so that the gaps between the moving friction plates 11 are equal, the moving friction plates 11 and the moving gasket 14 are fixed on the torque feedback shaft 5 through keys, and the static friction plate 12 and the static gasket 8 are arranged between the base 15 and the upper cover 2, and the st...
PUM
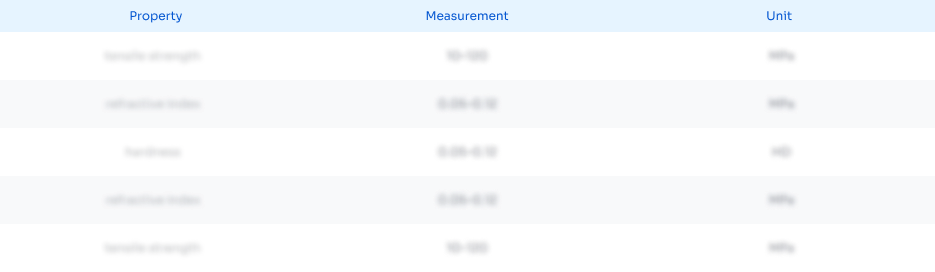
Abstract
Description
Claims
Application Information

- R&D Engineer
- R&D Manager
- IP Professional
- Industry Leading Data Capabilities
- Powerful AI technology
- Patent DNA Extraction
Browse by: Latest US Patents, China's latest patents, Technical Efficacy Thesaurus, Application Domain, Technology Topic, Popular Technical Reports.
© 2024 PatSnap. All rights reserved.Legal|Privacy policy|Modern Slavery Act Transparency Statement|Sitemap|About US| Contact US: help@patsnap.com