High-precision microvibration measuring system
A measurement system and micro-vibration technology, applied in measurement devices, measurement of ultrasonic/sonic/infrasonic waves, instruments, etc., can solve problems such as literature reports of micro-vibration measurement systems that have not been seen, and achieve improved measurement accuracy, improved adaptability, and improved reliability. sexual effect
- Summary
- Abstract
- Description
- Claims
- Application Information
AI Technical Summary
Problems solved by technology
Method used
Image
Examples
Embodiment Construction
[0023] Such as figure 1 As shown, the base 1, load plate 2, four piezoelectric sensors 3 installed in the vertical direction, four piezoelectric sensors 4 installed in the horizontal direction, four lateral positioning plates 5, eight bolts 6 and Data acquisition and processing system 7; four piezoelectric sensors 3 installed in the vertical direction are located between the upper surface of the base and the lower surface of the load plate, and are pressed by four bolts 6 to measure the vibration force in the Z direction and the X and Y directions Four lateral positioning plates 5 are fixed on the upper surface of the base 1 by screws; four piezoelectric sensors 4 installed in the horizontal direction are fixed on the lateral positioning plate 5 by four bolts 6 and nuts, four The installation direction of the piezoelectric sensor 4 installed in the horizontal direction is in a spatial vertical relationship with the Z axis to ensure that it can measure the vibration torque around...
PUM
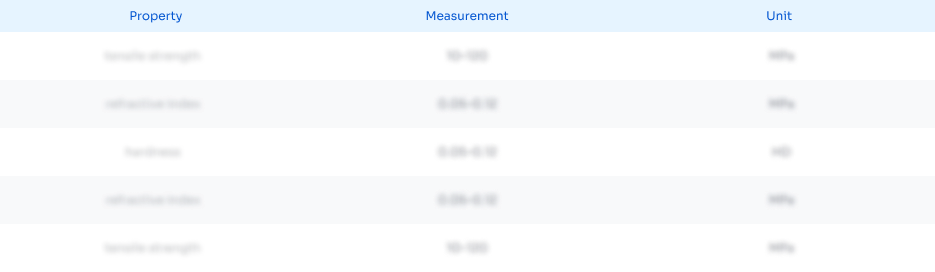
Abstract
Description
Claims
Application Information

- Generate Ideas
- Intellectual Property
- Life Sciences
- Materials
- Tech Scout
- Unparalleled Data Quality
- Higher Quality Content
- 60% Fewer Hallucinations
Browse by: Latest US Patents, China's latest patents, Technical Efficacy Thesaurus, Application Domain, Technology Topic, Popular Technical Reports.
© 2025 PatSnap. All rights reserved.Legal|Privacy policy|Modern Slavery Act Transparency Statement|Sitemap|About US| Contact US: help@patsnap.com