Electrostatic painting process of energy-saving lamp shade
An electrostatic spraying, energy-saving lamp technology, applied in coatings, devices for coating liquids on surfaces, surface pretreatment, etc., can solve problems such as environmental pollution, human health hazards, unfavorable promotion and application, and achieve broad application prospects and high Scratch resistance, the effect of significant technological progress
- Summary
- Abstract
- Description
- Claims
- Application Information
AI Technical Summary
Problems solved by technology
Method used
Examples
Embodiment 1
[0021] The electrostatic spraying process for lampshades of energy-saving lamps includes the following steps: firstly, cleaning the lampshades for subsequent spraying. Next, heat the glass bulb of the lampshade to reduce the specific resistance and conduct electricity. Specifically, the heating temperature of the lampshade glass bulb is set to 150°C. Subsequently, paint powder is sprayed on the inner wall of the lampshade. During this process, the spraying voltage is 50KV, and the machine speed is 6r / min. In order to make the spraying effect more stable, the electrostatic 16-station spray gun internal spraying machine can be used to spray the powder coating. Moreover, the powder suction airflow of the spray gun is 0.23Mpa, and the powder spray airflow is 0.18Mpa. At the same time, considering the uniform effect of spraying, the spray gun should be sprayed at least three times. Next, heat the sprayed lampshade to make the paint powder solidify and form a film. Specifically...
Embodiment 2
[0024] Electrostatic spraying process of energy-saving lamp lampshade: first, clean the lampshade. Next, heat the glass bulb of the lampshade to reduce the specific resistance and conduct electricity. Specifically, the heating temperature for the glass bulb of the lampshade is 400°C. Subsequently, paint powder is sprayed on the inner wall of the lampshade. During this process, the spraying voltage is 70KV, and the machine speed is 20r / min. In order to make the spraying effect more stable, the electrostatic 16-station spray gun internal spraying machine can be used to spray the powder coating. Moreover, the powder suction airflow of the spray gun is 0.28Mpa, and the powder spray airflow is 0.2Mpa. At the same time, considering the uniform effect of spraying, the spray gun should be sprayed at least three times. Finally, heat the sprayed lampshade to make the paint powder solidify and form a film. Specifically, a 48-station chain-type temperature-controlled curing machine c...
Embodiment 3
[0026] The electrostatic spraying process for lampshades of energy-saving lamps includes the following steps: firstly, cleaning the lampshades for subsequent spraying. Next, heat the glass bulb of the lampshade to reduce the specific resistance and conduct electricity. Specifically, the heating temperature of the lampshade glass bulb is set to 150°C. Subsequently, paint powder is sprayed on the inner wall of the lampshade. During this process, the spraying voltage is 50KV, and the machine speed is 15r / min. In order to make the spraying effect more stable, the electrostatic 16-station spray gun internal spraying machine can be used to spray the powder coating. Moreover, the powder suction airflow of the spray gun is 0.26Mpa, and the powder spray airflow is 0.2Mpa. At the same time, considering the uniform effect of spraying, the spray gun should be sprayed at least three times. Next, heat the sprayed lampshade to make the paint powder solidify and form a film. Specifically...
PUM
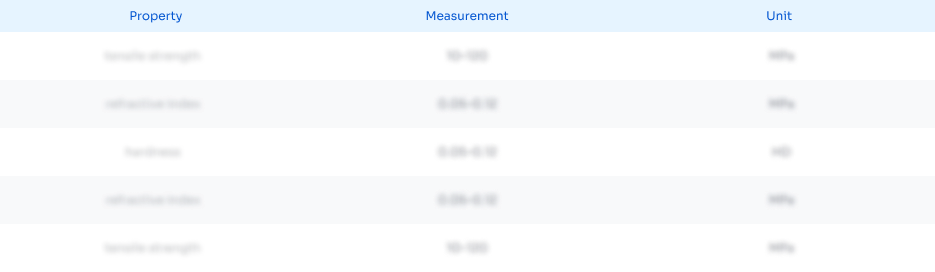
Abstract
Description
Claims
Application Information

- R&D
- Intellectual Property
- Life Sciences
- Materials
- Tech Scout
- Unparalleled Data Quality
- Higher Quality Content
- 60% Fewer Hallucinations
Browse by: Latest US Patents, China's latest patents, Technical Efficacy Thesaurus, Application Domain, Technology Topic, Popular Technical Reports.
© 2025 PatSnap. All rights reserved.Legal|Privacy policy|Modern Slavery Act Transparency Statement|Sitemap|About US| Contact US: help@patsnap.com