A bearing and method for transferring forces through a bearing of a wind turbine
A wind turbine and force transmission technology, applied in the direction of bearings, bearings, ball bearings and other directions of rotating motion, can solve problems such as increasing bearing degradation and shortening service life, and achieve the effect of reducing friction, reducing production and installation costs, and simplifying structure
- Summary
- Abstract
- Description
- Claims
- Application Information
AI Technical Summary
Problems solved by technology
Method used
Image
Examples
Embodiment Construction
[0041] figure 1 A modern wind turbine 1 is shown with a tower 2 and a wind turbine nacelle 3 on top of the tower 2 .
[0042] A wind turbine rotor is connected to the hub 4 via a pitch mechanism 6, said wind turbine rotor comprising at least one blade, for example as figure 1Three wind turbine blades 5 are shown. Each pitch mechanism includes a blade bearing and a separate pitch actuator that enables the blade to pitch. The pitch change process is controlled by the pitch controller.
[0043] Such as figure 1 As shown, wind above a certain level will actuate the rotor and cause the rotor to rotate in a direction substantially perpendicular to the wind direction. The rotational motion is converted into electrical power, which is typically supplied to a utility grid, as known to those skilled in the art.
[0044] figure 2 A front view of the wind turbine hub 4 is shown. The wind turbine rotor blade 5 is connected to the hub 4 through a pitch mechanism 6, and the pitch ...
PUM
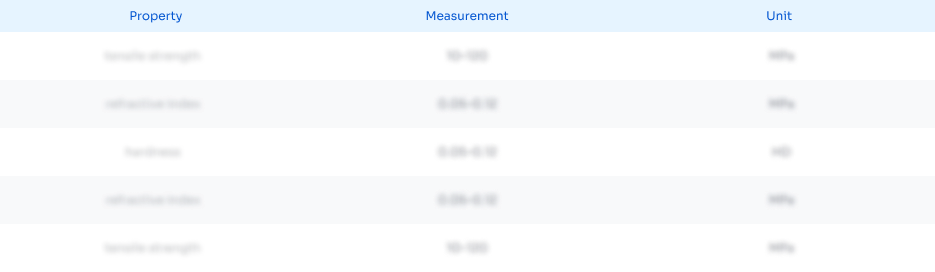
Abstract
Description
Claims
Application Information

- Generate Ideas
- Intellectual Property
- Life Sciences
- Materials
- Tech Scout
- Unparalleled Data Quality
- Higher Quality Content
- 60% Fewer Hallucinations
Browse by: Latest US Patents, China's latest patents, Technical Efficacy Thesaurus, Application Domain, Technology Topic, Popular Technical Reports.
© 2025 PatSnap. All rights reserved.Legal|Privacy policy|Modern Slavery Act Transparency Statement|Sitemap|About US| Contact US: help@patsnap.com