Billet-extruding central shaft
A technology of central shaft and connecting shaft, applied in the field of extruded central shaft, to achieve the effect of large self-weight vertical force, long suspension distance and ensuring levelness
- Summary
- Abstract
- Description
- Claims
- Application Information
AI Technical Summary
Problems solved by technology
Method used
Image
Examples
Embodiment Construction
[0013] see figure 1 . After the mud material enters the vacuum mud refining machine from the feed port 2, the power passes through the gear box 1 to make the upper main shaft 3 rotate, and the screw blade sends the mud material that has been initially refined and mixed into the vacuum chamber 44. In the vacuum chamber 44, the mud material falls into the area where the lower main shaft 4 is located, and the screw blade 41 pushes the mud material to move forward, and enters the process cylinder 6 from the outlet at the front end of the mud material output cylinder 43, and continuously moves forward, and finally from the inside The passage between the outer wall of the hole mold core 7 and the inner wall of the inner hole mold core barrel 71 is extruded to form a mud base product. The outer wall of the product is circular, and the shape of the inner hole is determined by the shape of the outer wall of the inner hole mold core 7. Therefore, the shape of the mud blank inner hole c...
PUM
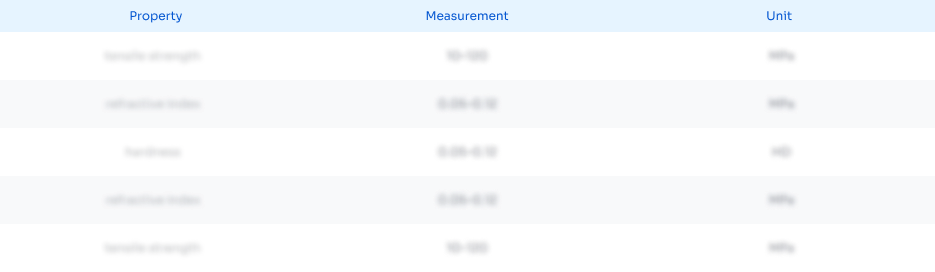
Abstract
Description
Claims
Application Information

- R&D Engineer
- R&D Manager
- IP Professional
- Industry Leading Data Capabilities
- Powerful AI technology
- Patent DNA Extraction
Browse by: Latest US Patents, China's latest patents, Technical Efficacy Thesaurus, Application Domain, Technology Topic, Popular Technical Reports.
© 2024 PatSnap. All rights reserved.Legal|Privacy policy|Modern Slavery Act Transparency Statement|Sitemap|About US| Contact US: help@patsnap.com