Elevator non-load traction capacity detecting method
A detection method and no-load technology, which is applied in the direction of elevators, transportation and packaging, etc., can solve the problems of consuming manpower and material resources, not being able to know the specific condition of traction force, and being large in use
- Summary
- Abstract
- Description
- Claims
- Application Information
AI Technical Summary
Problems solved by technology
Method used
Image
Examples
Embodiment Construction
[0050] Attached below figure 1 , figure 2 To further explain the present invention:
[0051] 1) Park the elevator car 7 in the middle of the hoistway, namely figure 2 Middle 3 and 4 are at the same height in the hoistway. Fix the car and counterweight wire ropes to prevent relative displacement between the wire ropes on both sides of the traction sheave 3, and install forces on the wire ropes on both sides of the traction sheave 3. Sensor a 9 and sensor b 10;
[0052] 2) Release the elevator traction machine brake 2 ( figure 1 In 2), adjust the motor shaft so that the gear of the reducer is in a free state. The purpose is to make the gear, worm gear, and worm gear meshed in the gearbox affect the free movement of the traction wheel as little as possible, and pass when the reading is stable. figure 2 The sensor marked in middle 2 reads the downward pulling force on the steel wire rope on the counterweight side. This value is the poor quality of the car and the counterweight. Its ...
PUM
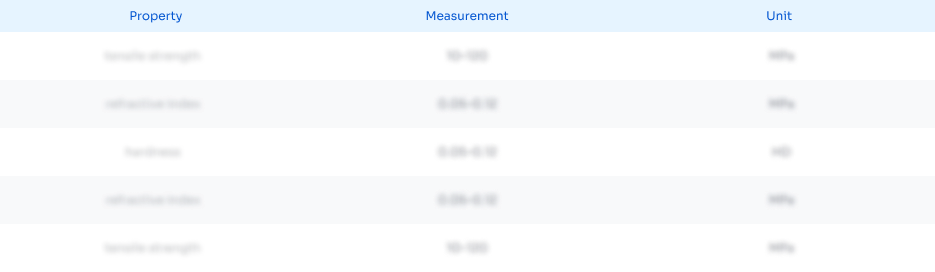
Abstract
Description
Claims
Application Information

- R&D Engineer
- R&D Manager
- IP Professional
- Industry Leading Data Capabilities
- Powerful AI technology
- Patent DNA Extraction
Browse by: Latest US Patents, China's latest patents, Technical Efficacy Thesaurus, Application Domain, Technology Topic, Popular Technical Reports.
© 2024 PatSnap. All rights reserved.Legal|Privacy policy|Modern Slavery Act Transparency Statement|Sitemap|About US| Contact US: help@patsnap.com