Device and method for detecting initial position angle of double fed electric machine rotor
A technology of rotor initial position and doubly-fed motor, which is applied in the field of detection, can solve the problems of difficult realization, large rotor moment of inertia, high motor requirements, etc., and achieves the effects of convenient use, easy operation, simple and reliable structure, and wide application range
- Summary
- Abstract
- Description
- Claims
- Application Information
AI Technical Summary
Problems solved by technology
Method used
Image
Examples
Embodiment Construction
[0012] The present invention will be further described below in conjunction with the embodiment in the accompanying drawings:
[0013] figure 1 Shown: The circuit is mainly composed of voltage detection circuit U2, U3, zero-crossing comparison circuit U4, photoelectric isolation circuit U5, U6, DSP processor U7, power supply circuit U8, clock circuit U9, watchdog circuit U10, JTAG interface circuit U11 . The voltage detection circuits U2 and U3 are respectively connected to the stator and rotor of the doubly-fed motor U1, and are respectively used to detect the induced electromotive force output by the stator and rotor sides of the doubly-fed motor U1, and convert the induced electromotive force into a weak current signal; the voltage detection circuit U2 and U3 are respectively connected to the zero-crossing comparison circuit U4, which converts the stator and rotor induced electromotive force detected by the voltage detection circuits U2 and U3 into square wave signals; the...
PUM
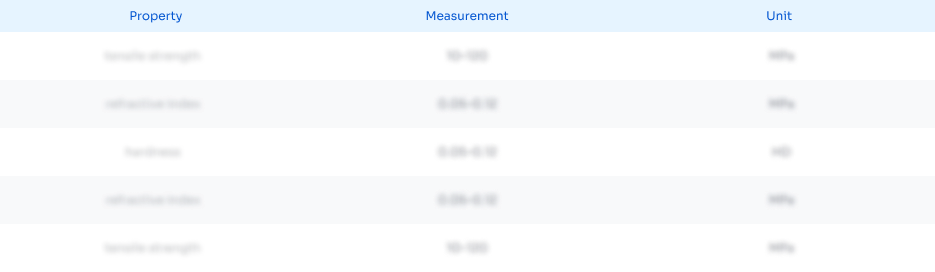
Abstract
Description
Claims
Application Information

- Generate Ideas
- Intellectual Property
- Life Sciences
- Materials
- Tech Scout
- Unparalleled Data Quality
- Higher Quality Content
- 60% Fewer Hallucinations
Browse by: Latest US Patents, China's latest patents, Technical Efficacy Thesaurus, Application Domain, Technology Topic, Popular Technical Reports.
© 2025 PatSnap. All rights reserved.Legal|Privacy policy|Modern Slavery Act Transparency Statement|Sitemap|About US| Contact US: help@patsnap.com