Servo system controller with self-adapting fuzzy frictional compensation
An adaptive fuzzy and friction compensation technology, which is applied in the field of precision motor servo system, can solve the problems that cannot meet the requirements of high precision and fast response of the servo system, make accurate compensation of the difficult motor servo system, and cannot guarantee the system control performance. The effect of offsetting unknown friction, ensuring closed-loop stability, and fast friction model identification speed
- Summary
- Abstract
- Description
- Claims
- Application Information
AI Technical Summary
Problems solved by technology
Method used
Image
Examples
Embodiment Construction
[0024] The invention provides an adaptive fuzzy friction compensation method of a motor servo system. Embodiments of the present invention will be described in detail below with reference to the accompanying drawings.
[0025] figure 1 is a block diagram of a servo system controller with adaptive fuzzy friction compensation. The servo system controller with adaptive fuzzy friction compensation includes: a robust control module, a parameter adaptive adjustment module, and a fuzzy friction compensator. The servo system controller with adaptive fuzzy friction compensation can be realized by embedded processors such as digital signal processors (eg: TMS320F2812, TMS320LF2407), 8051 single-chip microcomputers and their peripheral circuits. Since the algorithm proposed by the present invention is a continuous time algorithm, the software implementation in the embedded processor needs to use numerical methods such as Runge-Kutta method and Euler method to convert the continuous tim...
PUM
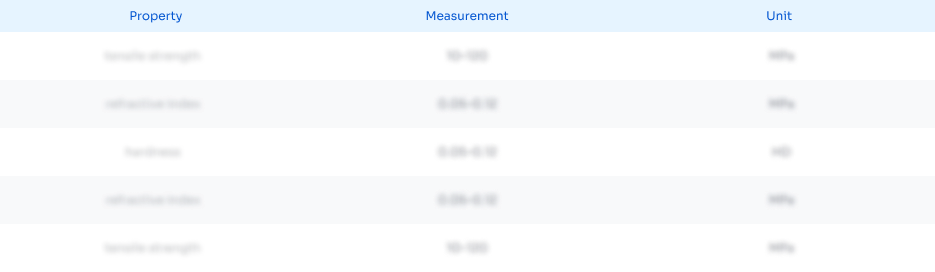
Abstract
Description
Claims
Application Information

- R&D
- Intellectual Property
- Life Sciences
- Materials
- Tech Scout
- Unparalleled Data Quality
- Higher Quality Content
- 60% Fewer Hallucinations
Browse by: Latest US Patents, China's latest patents, Technical Efficacy Thesaurus, Application Domain, Technology Topic, Popular Technical Reports.
© 2025 PatSnap. All rights reserved.Legal|Privacy policy|Modern Slavery Act Transparency Statement|Sitemap|About US| Contact US: help@patsnap.com