Double arm robot
A robot and dual-arm technology, applied in the field of robotics, can solve the problems of longer transfer period, inability to move up and down independently, and inability to change the distance between the two arms, so as to suppress adverse particles or vibrations, eliminate adverse effects, and improve The effect of transport efficiency
- Summary
- Abstract
- Description
- Claims
- Application Information
AI Technical Summary
Problems solved by technology
Method used
Image
Examples
Embodiment 1
[0050] figure 1 It is a perspective view showing the overall structure of the dual-arm robot of the present invention.
[0051] The double-armed robot 1 of the present invention is provided with two sets of shoulder joints 3, elbow joints 4, and hand joints 5, which are rotatably connected, transmit the rotational force of the rotational drive source, and perform desired actions at various levels. Articulated Arm2. In addition, the hand 8 mounted on the tip of the arm 2 for placing workpieces moves linearly through the arm 2 in the telescopic direction (X-axis direction of the Cartesian coordinate system) shown in the figure, and carries out loading and unloading of workpieces such as stockers. Move out.
[0052] 101 and 102 are arm support members, and 101 is configured to suspend one arm, and 102 is configured to support the other arm. The arms 2 are connected to the supporting member 101 or 102 via the respective shoulder joints 3 , and as a result, the two arms are arr...
PUM
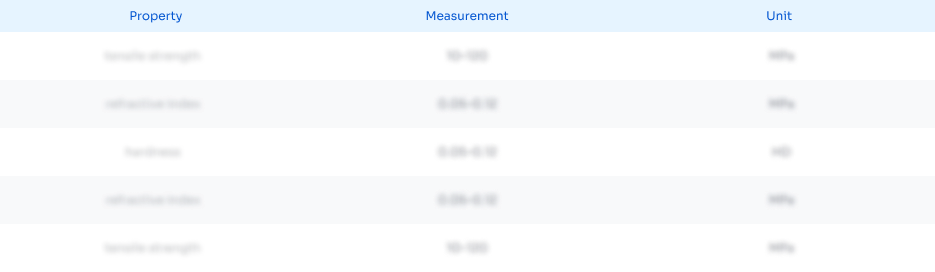
Abstract
Description
Claims
Application Information

- R&D Engineer
- R&D Manager
- IP Professional
- Industry Leading Data Capabilities
- Powerful AI technology
- Patent DNA Extraction
Browse by: Latest US Patents, China's latest patents, Technical Efficacy Thesaurus, Application Domain, Technology Topic, Popular Technical Reports.
© 2024 PatSnap. All rights reserved.Legal|Privacy policy|Modern Slavery Act Transparency Statement|Sitemap|About US| Contact US: help@patsnap.com