Process for the production of a cellulosic fiber from a solution of cellulose in a tertiary amine-oxide and device for carrying out said process
A cellulose solution, tertiary amine oxide technology, applied in the direction of single-component cellulose rayon, fiber chemical characteristics, textiles and papermaking, etc., can solve the problem of reducing equipment output, increasing fiber production costs, and unable to start the spinning process And other issues
- Summary
- Abstract
- Description
- Claims
- Application Information
AI Technical Summary
Problems solved by technology
Method used
Image
Examples
Embodiment Construction
[0041] The present invention will be described more fully hereinafter with reference to the accompanying drawings, in which preferred embodiments of the invention are shown.
[0042]The process of producing cellulose fibers from cellulose solutions in tertiary amine oxides by the spray-wet process generally includes several steps that have a significant effect on the structure and texture of the filaments. A first embodiment of an apparatus 1 suitable for carrying out the process is as Figure 1A shown. First, the cellulose solution is extruded through a spinneret (not shown), which may include one or more openings arranged in various configurations, such as one or more circular holes, and the like. Alternatively, the spinneret is a rectangular spinneret for spinning the filaments into a curtain form.
[0043] The filaments 2 thus obtained are guided through the air gap 3 between the spinneret and the vessel 4 containing the precipitation bath. While passing through the air ...
PUM
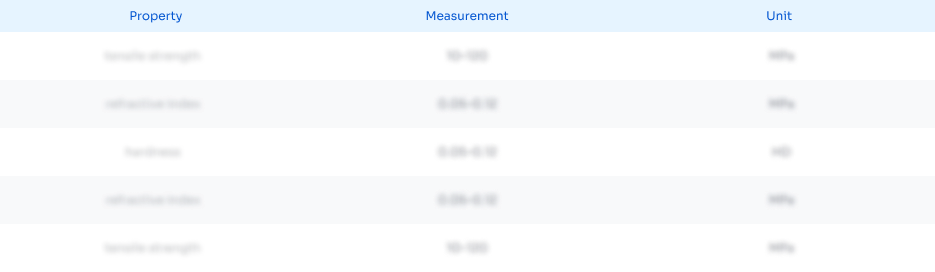
Abstract
Description
Claims
Application Information

- Generate Ideas
- Intellectual Property
- Life Sciences
- Materials
- Tech Scout
- Unparalleled Data Quality
- Higher Quality Content
- 60% Fewer Hallucinations
Browse by: Latest US Patents, China's latest patents, Technical Efficacy Thesaurus, Application Domain, Technology Topic, Popular Technical Reports.
© 2025 PatSnap. All rights reserved.Legal|Privacy policy|Modern Slavery Act Transparency Statement|Sitemap|About US| Contact US: help@patsnap.com