Self-twisting hollow ingot special for jet air vortex spinning
A technology of hollow spindle and vortex spinning, which is applied to spinning machines, textiles and papermaking, and open-end spinning machines, etc. It can solve the problems of many details, low strength, and poor yarn structure, so as to reduce loss and increase strength , the effect of reducing production costs
- Summary
- Abstract
- Description
- Claims
- Application Information
AI Technical Summary
Problems solved by technology
Method used
Image
Examples
Embodiment 1
[0017] Such as figure 1 , 2 As shown, a special self-twisting hollow spindle for air-jet vortex spinning includes a fiber inlet 1 and a hollow spindle channel 2, and the fiber inlet 1 and the hollow spindle channel 2 are provided with 4 holes with the fiber inlet 1 and the hollow spindle channel 2. The center of the circle is a linear surface groove 3 distributed in a central circular array, and the diameter D of the fiber inlet 1 is 1 3mm, diameter D of hollow ingot channel 2 2 1.2mm, the width D of surface groove 3 3 0.1mm, the height H from the fiber inlet to the hollow ingot channel 1 8mm, hollow ingot channel height H 2 4mm, surface groove height H 3 is 0.1 mm, the chamfer angle θ of the fiber entrance 1 is 30°, and the inner surface of the surface groove 3 is streamlined.
Embodiment 2
[0019] Such as figure 1 , 3 As shown, a self-twisting hollow spindle dedicated to air-jet vortex spinning includes a fiber inlet 1 and a hollow spindle passage 2, and eight fiber inlets 1 and hollow spindle passages 2 are provided on the fiber inlet 1 and hollow spindle passage 2. The center of the circle is the arc-shaped surface groove 3 distributed in the central circular array, and the diameter D of the fiber inlet 1 is 1 4mm, diameter D of hollow ingot channel 2 2 1.4mm, the width D of surface groove 3 3 0.4mm, the height H from the fiber entrance to the hollow ingot channel 1 9mm, hollow ingot channel height H 2 5mm, surface groove height H 3 is 0.4 mm, the chamfer angle θ of the fiber entrance 1 is 45°, and the inner surface of the surface groove 3 is streamlined.
Embodiment 3
[0021] Such as figure 1 , 3 As shown, a special self-twisting hollow spindle for air-jet vortex spinning includes a fiber inlet 1 and a hollow spindle channel 2, and the fiber inlet 1 and the hollow spindle channel 2 are provided with 6 holes with the fiber inlet 1 and the hollow spindle channel 2. The center of the circle is the arc-shaped surface groove 3 distributed in the central circular array, and the diameter D of the fiber inlet 1 is 1 5mm, diameter D of hollow ingot channel 2 2 1.6mm, the width D of surface groove 3 3 0.8mm, the height H from the fiber inlet to the hollow ingot channel 1 10mm, hollow ingot channel height H 2 6mm, surface groove height H 3 is 1 mm, the chamfer angle θ of the fiber entrance 1 is 60°, and the inner surface of the surface groove 3 is streamlined.
PUM
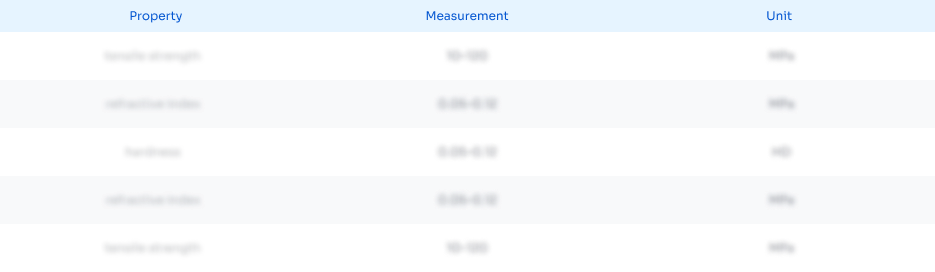
Abstract
Description
Claims
Application Information

- R&D
- Intellectual Property
- Life Sciences
- Materials
- Tech Scout
- Unparalleled Data Quality
- Higher Quality Content
- 60% Fewer Hallucinations
Browse by: Latest US Patents, China's latest patents, Technical Efficacy Thesaurus, Application Domain, Technology Topic, Popular Technical Reports.
© 2025 PatSnap. All rights reserved.Legal|Privacy policy|Modern Slavery Act Transparency Statement|Sitemap|About US| Contact US: help@patsnap.com