Method for preparing pigment grade chromium hemitrioxide green by using gaseous reducing agent to reduce chromate salt under low temperature
A technology of chromium oxide green and reducing agent, which is applied in the direction of chromium oxide/hydrate, fibrous filler, etc., can solve the problems of complex reaction equipment, high reaction temperature, and large energy consumption, and achieve simple equipment, mild process conditions, and realization of The effect of zero emissions
- Summary
- Abstract
- Description
- Claims
- Application Information
AI Technical Summary
Problems solved by technology
Method used
Image
Examples
Embodiment 1
[0014] The reduction of 100kg of potassium chromate is carried out in an electrothermal rotary reduction furnace, using hydrogen as the reducing gas, the reduction temperature is 450°C, the reduction time is 2h, and the hydrogen flow rate during the reduction process is 40Nm 3 / h.
[0015] After the reduction product is cooled, three-stage countercurrent washing is used. The liquid-solid volume ratio during the washing process is 1.00-1.05, and the washing temperature is 60°C. After washing, use a plate and frame filter press to filter, the moisture content of the filter cake is about 25%, and the filtered liquid recovers KOH for recycling. filter cake with 0.5wt% P 2 o 3 、HBO 3 , Zn(NO 3 ) 2 , SiO 2 、TiO 2 Ball milling and mixing in a ball mill, and the mixed material enters a rotary kiln for activation and sintering at a sintering temperature of 900°C and a sintering time of 3 hours. After sintering, the material is countercurrent washed, spin flash dried, and after ...
Embodiment 2
[0017] The reduction of 100kg of sodium chromate is carried out in an electrothermal rotary reduction furnace, using natural gas as the reducing gas, the reduction temperature is 400°C, the reduction time is 1.5h, and the natural gas flow rate during the reduction process is 60Nm 3 / h.
[0018] After the reduction product is cooled, three-stage countercurrent washing is used. The liquid-solid volume ratio during the washing process is 1.00-1.05, and the washing temperature is 70°C. After washing, use a plate and frame filter press to filter, the moisture content of the filter cake is about 25%, and the filtered liquid recovers NaOH for recycling. filter cake with 1.0wt% Al 2 o 3 、H 3 PO 4 , SiO 2 、K 2 TiO 3 , Sb 2 o 3 , ZnO is ball milled and mixed in a ball mill, and the mixed material is sent into a rotary kiln for activation and sintering at a sintering temperature of 950°C and a sintering time of 2.5 hours. After sintering, the material is countercurrent washed, ...
Embodiment 3
[0020] The reduction of 100kg of potassium chromate is carried out in an electrothermal rotary reduction furnace, using coal gas as the reducing gas, the reduction temperature is 500°C, the reduction time is 1h, and the gas flow rate during the reduction process is 80Nm 3 / h.
[0021] After the reduction product is cooled, three-stage countercurrent washing is used. The liquid-solid volume ratio during the washing process is 1.00-1.05, and the washing temperature is 80°C. After washing, use a plate and frame filter press to filter, the moisture content of the filter cake is about 25%, and the filtered liquid recovers KOH for recycling. filter cake with 1.5wt% H 3 PO 4 , Al(OH) 3 、TiO 2 , SiO 2 , ZnO is ball milled and mixed in a ball mill, and the mixed material is sent into a rotary kiln for activation and sintering. The sintering temperature is 1000°C and the sintering time is 2h. After sintering, the material is countercurrent washed, spin flash dried, and after dryin...
PUM
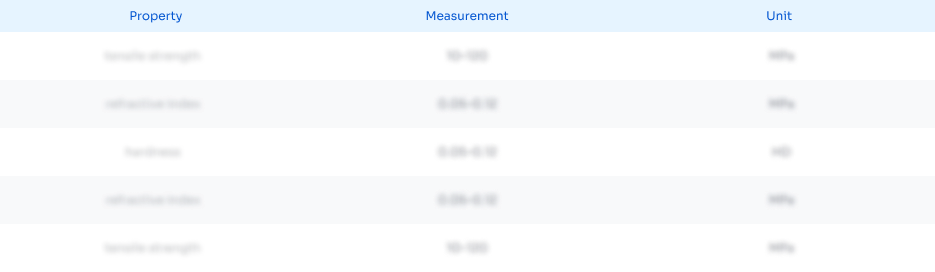
Abstract
Description
Claims
Application Information

- R&D
- Intellectual Property
- Life Sciences
- Materials
- Tech Scout
- Unparalleled Data Quality
- Higher Quality Content
- 60% Fewer Hallucinations
Browse by: Latest US Patents, China's latest patents, Technical Efficacy Thesaurus, Application Domain, Technology Topic, Popular Technical Reports.
© 2025 PatSnap. All rights reserved.Legal|Privacy policy|Modern Slavery Act Transparency Statement|Sitemap|About US| Contact US: help@patsnap.com