Method and device for controlling flatness of steel material
A control method and flatness technology, applied in electrical program control, program control in sequence/logic controllers, manufacturing tools, etc., can solve the problems affecting the production process, poor follow-up of pinch rollers and supporting rollers, stuck, etc. problems, to achieve the effect of convenient measurement and use, high measurement accuracy, and prevention of jamming
- Summary
- Abstract
- Description
- Claims
- Application Information
AI Technical Summary
Problems solved by technology
Method used
Image
Examples
Embodiment Construction
[0020] The present invention will be described in detail below in conjunction with the following embodiments and accompanying drawings.
[0021] Control method of the present invention:
[0022] The actual linear displacement of the pinch wheel 11 is measured by the rotary encoder installed at the tail of the linear displacement servo motor 1, and the actual rotation angle of the pinch wheel 11 is measured by the rotary encoder installed at the tail of the corner servo motor 2. These measurements are obtained The signal is converted into a TTL square wave pulse by the transmitter inside the rotary encoder and sent to the counting card with the function of adding and subtracting counting in the industrial computer, and then calculate the linear displacement and rotation angle of the pressing wheel through the functional relationship; the counting card has 3 counting channels, plugged into the ISA bus slot of the industrial computer; the analog output card has 6 analog output ch...
PUM
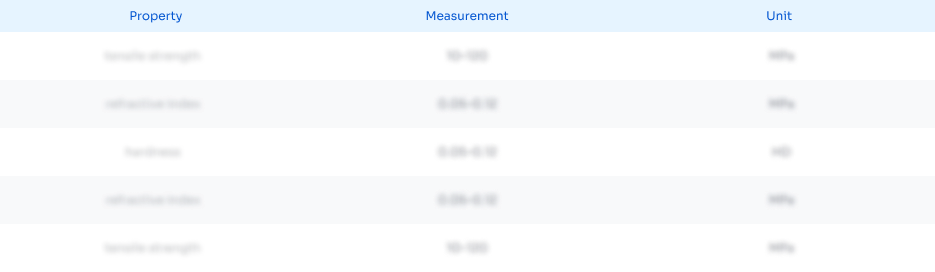
Abstract
Description
Claims
Application Information

- R&D Engineer
- R&D Manager
- IP Professional
- Industry Leading Data Capabilities
- Powerful AI technology
- Patent DNA Extraction
Browse by: Latest US Patents, China's latest patents, Technical Efficacy Thesaurus, Application Domain, Technology Topic, Popular Technical Reports.
© 2024 PatSnap. All rights reserved.Legal|Privacy policy|Modern Slavery Act Transparency Statement|Sitemap|About US| Contact US: help@patsnap.com