Self-wind cooled rotor magneto resistance genus motor
A rotor and stator technology, applied in the field of self-wind cooling rotor reluctance motors, can solve the problems of stator, rotor temperature rise, eddy current loss, affecting winding life, etc., to improve the working magnetic flux density, reduce volume weight, reduce Effect of heat dissipation area
- Summary
- Abstract
- Description
- Claims
- Application Information
AI Technical Summary
Problems solved by technology
Method used
Image
Examples
Embodiment Construction
[0021] specific implementation plan
[0022] Taking the doubly salient pole motor as an example, since the rotor of the doubly salient pole motor has only salient pole teeth and cogging, and there is no winding, the present invention proposes to use the structural characteristics of the salient pole teeth and cogging to make the salient pole of the doubly salient pole motor rotor The teeth are designed as the blade structure shape of the axial flow fan, so that when the rotor rotates, the air around one end of the rotor (inlet end) can be sucked into the tooth groove of the motor rotor, and then go out from the other end of the rotor (air outlet end), directly taking away the motor. The heat generated by the rotor thus cools the motor. In order to achieve this purpose, the shape of the salient pole teeth of the rotor can be designed according to the working principle of the blades of the axial flow fan.
[0023] figure 1 and figure 2 It is a schematic diagram of the rotor ...
PUM
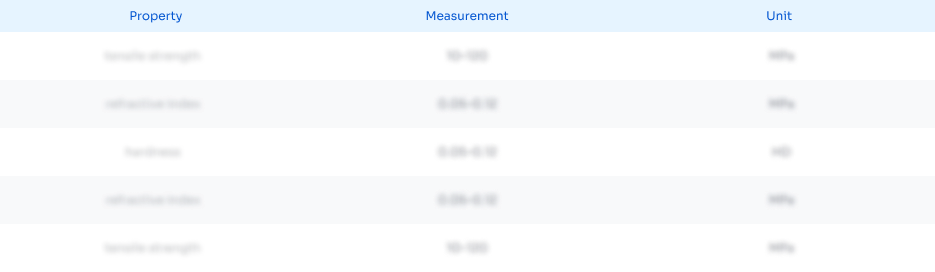
Abstract
Description
Claims
Application Information

- R&D
- Intellectual Property
- Life Sciences
- Materials
- Tech Scout
- Unparalleled Data Quality
- Higher Quality Content
- 60% Fewer Hallucinations
Browse by: Latest US Patents, China's latest patents, Technical Efficacy Thesaurus, Application Domain, Technology Topic, Popular Technical Reports.
© 2025 PatSnap. All rights reserved.Legal|Privacy policy|Modern Slavery Act Transparency Statement|Sitemap|About US| Contact US: help@patsnap.com