Extruders for degassing and filtering plastic melts
A melt and filter technology, applied in the field of devices for extruding thermoplastic materials, can solve the problems of device pressure fluctuations, the same quality of plastics that cannot be degassed and purified, etc., and achieves the effect of improving degassing effect.
- Summary
- Abstract
- Description
- Claims
- Application Information
AI Technical Summary
Problems solved by technology
Method used
Image
Examples
Embodiment Construction
[0011] The device for extruding thermoplastic materials comprises an extrusion screw 2 mounted in a housing 1 , which has an inlet-side plasticizing section P and a degassing section E upstream of the outlet section A. Between the plasticizing section P and the degassing section E, a counter-conveying flight 3 and a flow channel 5 bridging the counter-conveying course 3 and containing a melt filter 4 are provided. In order to prevent the gas generated in the plasticizing section from overflowing directly into the degassing section, the extrusion screw 2 is formed in the same direction between the reverse conveying screw 3 and the outlet 6 in the degassing section E on the discharge side of the flow channel 5 The conveying screw 7, and the shell 1 is provided with a degassing hole 8 in the transitional part between the reverse and the same direction conveying screw 3, 7, through which the gas and dirt squeezed into the conveying screw part from the device 1 The medium is advant...
PUM
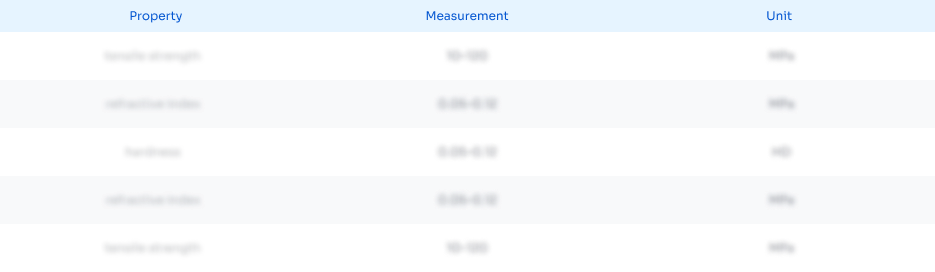
Abstract
Description
Claims
Application Information

- R&D Engineer
- R&D Manager
- IP Professional
- Industry Leading Data Capabilities
- Powerful AI technology
- Patent DNA Extraction
Browse by: Latest US Patents, China's latest patents, Technical Efficacy Thesaurus, Application Domain, Technology Topic, Popular Technical Reports.
© 2024 PatSnap. All rights reserved.Legal|Privacy policy|Modern Slavery Act Transparency Statement|Sitemap|About US| Contact US: help@patsnap.com