Silk broadcloth non-methanal discharge printing discharge paste and its discharge printing technique
A discharge printing and formaldehyde technology, applied in the field of formaldehyde-free discharge printing discharge paste and preparation, can solve the problems of large consumption, reduced processing cost, high cost, etc., and achieve the effect of low consumption and light washing task
- Summary
- Abstract
- Description
- Claims
- Application Information
AI Technical Summary
Problems solved by technology
Method used
Image
Examples
Embodiment 1
[0036] (1) Fabric preparation: silk crepe chine fabric dyed with weakly acid brilliant orange GS dye.
[0037] (2) Preparation of the original paste: Add 24g of the modified plant seed glue A9 paste into a 500ml beaker, then add 276ml of water, and stir until the paste is uniform.
[0038] (3) Preparation of white pulp: add 70 g of the above-mentioned raw paste into a 200 ml beaker, then add 5 g of urea, 5 g of thiourea dioxide, and 20 g of water, and stir evenly to make white pulp.
[0039] (4) Preparation of color drawing pulp: Add 2 g of engraved ON yellow, a flower color dye, and 18 ml of hot water into a 50 ml beaker, and stir until the dye is completely dissolved. Add 70g of the above-mentioned modified seed gum A9 paste into a 200ml beaker, then add 5g of urea, 5g of thiourea dioxide and ON yellow solution of flower color dye, and stir evenly to make color drawing pulp.
[0040] (5) Printing on silk crepe chine fabric dyed with weakly acid brilliant orange GS dye with ...
Embodiment 2
[0045] (1) Fabric preparation: silk crepe chine fabric dyed with weak acid dark blue 5R dye.
[0046] (2) Preparation of raw paste: Add 39g of modified plant seed glue A13 paste into a 500ml beaker, then add 261ml of water, and stir until the paste is uniform.
[0047] (3) Add 60 g of the above-mentioned raw paste into a 200 ml beaker, then add 4 g of urea, 7 g of thiourea dioxide and 29 ml of water, and stir evenly to make white paste.
[0048] (4) Preparation of color drawing pulp: Add 2 g of engraving G red, the color dye, and 25 ml of hot water into a 50 ml beaker, and stir until the dye is completely dissolved. Add 62g of the above-mentioned raw paste into a 200ml beaker, then add 4g of urea, 7g of thiourea dioxide and the above-mentioned floral dye engraving G red solution, and stir evenly to make a color drawing paste.
[0049] (5) Printing on silk crepe chine fabric dyed with weakly acidic dark blue 5R dye with white pulp and colored pulp respectively.
[0050] (6) D...
Embodiment 3
[0054] (1) Fabric preparation: silk crepe chine fabric dyed with Kapron pink BS dye.
[0055](2) Raw paste preparation: Add 150g of thickening slurry containing 3% synthetic thickener PT-RV and 150g of thickening slurry containing 3.5% synthetic thickener PFL into a 500ml beaker, stir evenly to make a pull-resistant Compound thickener. (3) Add 75g of the above-mentioned composite thickening pulp into a 200ml beaker, then add 6g of urea, 5g of thiourea dioxide and 14ml of water, and stir evenly to make white pulp.
[0056] (4) Preparation of color drawing pulp: Add 2 g of engraved BL blue and 14 ml of hot water into a 50 ml beaker, and stir until the dye is completely dissolved. Add 75g of the above-mentioned composite thickening paste into a 200ml beaker, then add 6g of urea, 3g of thiourea dioxide and the above-mentioned floral dye engraving BL blue solution, and stir evenly to make a color drawing paste.
[0057] (5) Printing on silk crepe chine fabric dyed with Kapron pin...
PUM
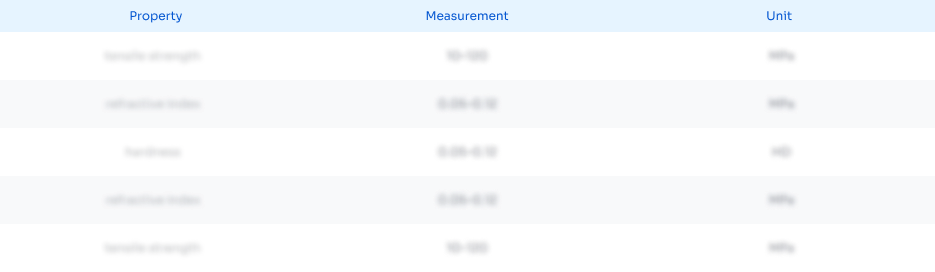
Abstract
Description
Claims
Application Information

- Generate Ideas
- Intellectual Property
- Life Sciences
- Materials
- Tech Scout
- Unparalleled Data Quality
- Higher Quality Content
- 60% Fewer Hallucinations
Browse by: Latest US Patents, China's latest patents, Technical Efficacy Thesaurus, Application Domain, Technology Topic, Popular Technical Reports.
© 2025 PatSnap. All rights reserved.Legal|Privacy policy|Modern Slavery Act Transparency Statement|Sitemap|About US| Contact US: help@patsnap.com