Catalyst for producing city gas with natural gas intermittent conversion and method of producing the same
A city gas and catalyst technology, which is applied to the catalyst field of natural gas steam reforming, can solve the problems of high raw material purity requirements, high raw material cost and high operating cost, and achieve the effects of high conversion activity, high resistance to carbon deposition and low cost.
- Summary
- Abstract
- Description
- Claims
- Application Information
AI Technical Summary
Problems solved by technology
Method used
Image
Examples
Embodiment 1
[0030] In this embodiment, the following method is used to prepare SiO 2 -Al 2 O 3 Composite oxide carrier:
[0031] Take kaolin and alumina as raw materials, weigh kaolin (of which Al 2 O 3 With SiO 2 The mass ratio is 1:1.13)50g, Al 2 O 3 141g, after mechanical ball milling to a particle size greater than 200 mesh, add proper amount of water and roll into a ball with φ19mm. After drying, calcining at 1300℃ for 4 hours, then SiO is obtained 2 -Al 2 O 3 Composite oxide carrier. The main phase of the carrier is α-Al 2 O 3 And Al 6 Si 2 O 13 Etc. Al in the carrier 2 O 3 With SiO 2 The mass ratio is 1:0.138; the relevant physical properties of the carrier are shown in Table 1 below:
[0032] Table 1 SiO 2 -Al 2 O 3 Physical properties of composite oxide carrier
[0033]
Embodiment 2
[0035] In this embodiment, the following method is used to prepare SiO 2 -Al 2 O 3 Composite oxide carrier:
[0036] Take kaolin and alumina as raw materials, weigh kaolin (of which Al 2 O 3 With SiO 2 The mass ratio is 1:1.13)50g, Al 2 O 3 201.4g, after mechanical ball milling to a particle size greater than 200 mesh, add appropriate amount of water and roll it into a φ19mm spherical shape. After drying, calcining at 1300℃ for 4 hours, then SiO is obtained 2 -Al 2 O 3 Composite oxide carrier. The main phase of the carrier is α-Al 2 O 3 And Al 6 Si 2 O 13 Etc. Al in the carrier 2 O 3 With SiO 2 The mass ratio is 1:0.1.
Embodiment 3
[0038] In this embodiment, the following method is used to prepare SiO 2 -Al 2 O 3 Composite oxide carrier:
[0039] Take kaolin and alumina as raw materials, weigh kaolin (of which Al 2 O 3 With SiO 2 The mass ratio is 1:1.13)50g, Al 2 O 3 29.6g, after mechanical ball milling to a particle size greater than 200 mesh, add proper amount of water and roll into a ball with φ19mm. After drying, calcining at 1300℃ for 4 hours, then SiO is obtained 2 -Al 2 O 3 Composite oxide carrier. The main phase of the carrier is α-Al 2 O 3 And Al 6 Si 2 O 13 Etc. Al in the carrier 2 O 3 With SiO 2 The mass ratio is 1:0.45.
[0040] Through measurement, the physical performance indexes of the catalyst carrier obtained in Examples 2 and 3, such as the strength and water pore volume, are not much different from the corresponding indexes of the catalyst carrier obtained in Example 1.
PUM
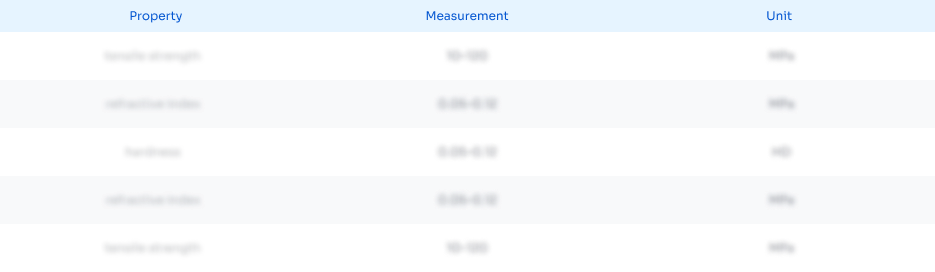
Abstract
Description
Claims
Application Information

- R&D
- Intellectual Property
- Life Sciences
- Materials
- Tech Scout
- Unparalleled Data Quality
- Higher Quality Content
- 60% Fewer Hallucinations
Browse by: Latest US Patents, China's latest patents, Technical Efficacy Thesaurus, Application Domain, Technology Topic, Popular Technical Reports.
© 2025 PatSnap. All rights reserved.Legal|Privacy policy|Modern Slavery Act Transparency Statement|Sitemap|About US| Contact US: help@patsnap.com