Hot-forming die, press-forming device, and hot press-forming method
一种冲压成形、热成形的技术,应用在成型工具、制造工具、金属加工设备等方向,能够解决更换作业麻烦、冷却时间延迟、增加成本等问题,达到容易维护保养、强度优良的效果
- Summary
- Abstract
- Description
- Claims
- Application Information
AI Technical Summary
Problems solved by technology
Method used
Image
Examples
Embodiment 1
[0036] First, use figure 1 The forming apparatus of this embodiment will be described. in, figure 1 A schematic diagram showing the press forming apparatus of this embodiment.
[0037] figure 1 Among them, the punch 1 as the upper die can move along the arrow Y direction ( figure 1 In the up and down direction, that is, the up and down direction of the forming device) displacement. Furthermore, a die 2 serving as a lower die is fixed to a plate 3 . Such as figure 1 As shown by the dotted line of , supply passages (a main supply passage 10 a and branch supply passages 10 b to be described later) through which the coolant passes are provided inside the die 2 .
[0038] The flat metal plate 4 heated to 700 to 1000° C. by a heating furnace (not shown) is conveyed to the forming apparatus 5 having the above-mentioned structure by a conveying mechanism including a conveying robot or the like. When the metal plate 4 is placed on the die 2, the punch 1 is lowered.
[0039] Whe...
Embodiment 2
[0081] use below Figure 5 A forming apparatus according to Example 2 of the present invention will be described. in, Figure 5 It is a diagram showing a part of the die 2 , that is, an internal structure around a recess formed in the die 2 .
[0082] Only the parts different from the first embodiment will be described below, and the configurations not described are the same as those of the first embodiment. In this embodiment, the structure of the nozzle member and the branch supply passage is partly different from that of Embodiment 1.
[0083] The nozzle member 12 is formed of an elastically deformable material (for example, resin, rubber, ceramics, cork, glass), and the same passage hole as in the first embodiment is formed inside. Furthermore, the outer peripheral surface of the nozzle member 12 is substantially cylindrical.
[0084] The branch supply passage 10b has approximately the same diameter in all areas. That is, unlike the structure of Example 1, no threaded...
Embodiment 3
[0090] Below, use Figure 6 with Figure 7 A forming apparatus according to Example 3 of the present invention will be described. in, Figure 6 (A) is a longitudinal sectional view of the nozzle member used in the present embodiment, Figure 6 (B) is from one end ( Figure 6 (A) The direction of the arrow A1) The external view when looking at the nozzle part. and, Figure 7 (A) is a longitudinal sectional view of a nozzle member of another form of the present invention, Figure 7 (B) is from one end side ( Figure 7 (A) The direction of the arrow A2) The external view of the nozzle part.
[0091] Only the parts different from the first embodiment will be described below, and the configurations not described are the same as those of the first embodiment. In this embodiment, the structure of the nozzle member is different from Embodiment 1.
[0092] On the outer peripheral surface of the nozzle member 13, a threaded portion 10d formed on the inner peripheral surface of ...
PUM
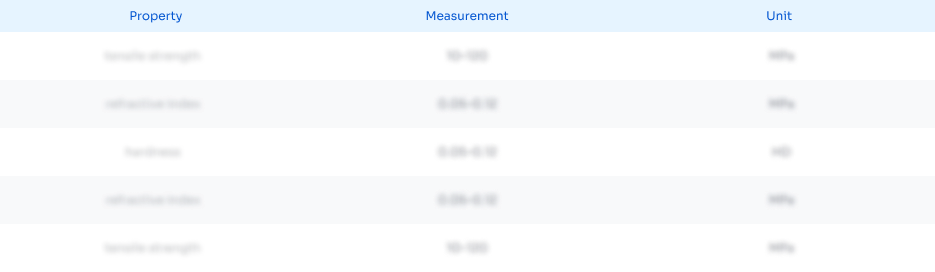
Abstract
Description
Claims
Application Information

- R&D Engineer
- R&D Manager
- IP Professional
- Industry Leading Data Capabilities
- Powerful AI technology
- Patent DNA Extraction
Browse by: Latest US Patents, China's latest patents, Technical Efficacy Thesaurus, Application Domain, Technology Topic, Popular Technical Reports.
© 2024 PatSnap. All rights reserved.Legal|Privacy policy|Modern Slavery Act Transparency Statement|Sitemap|About US| Contact US: help@patsnap.com