Longitudinal-shaking sandwich energy converter type cylinder shape dual rotor ultrasonic motor
A technology of ultrasonic motors and transducers, applied in the direction of generators/motors, piezoelectric effect/electrostrictive or magnetostrictive motors, electrical components, etc., to eliminate adverse effects, improve controllability, and simplify structures Effect
- Summary
- Abstract
- Description
- Claims
- Application Information
AI Technical Summary
Problems solved by technology
Method used
Image
Examples
specific Embodiment approach 1
[0012] Specific implementation mode one: see Figure 1 to Figure 11, this embodiment is composed of a stator assembly 1, an inner rotor assembly, an outer rotor assembly, a bearing housing 4, a bearing 5, a bearing preload end cover 6, a second screw group 7 and a third screw group 8; the stator assembly 1 is composed of The driving cylinder 1-6 is composed of 2n bending vibration sandwich transducers 1-7, wherein n is a natural number greater than 1, and the 2n bending vibration sandwich transducers 1-7 are symmetrically distributed and fixedly connected to the driving circle Outside the side wall of the barrel 1-6, the bending vibration sandwich transducer 1-7 consists of a front end cover 1-6-2, a rear end cover 1-1, an insulating sleeve 1-2, and two pairs of piezoelectric ceramic sheets 1-3 , flange 1-4 and two pairs of copper electrode sheets 1-5, the front end cover 1-6-2 and the rear end cover 1-1 are quadrangular prisms whose sections are all rectangular and tapered, a...
specific Embodiment approach 2
[0014] Specific implementation mode two: see Figure 5 The difference between this embodiment and the first embodiment is that the cylinder 1-6-1, the front end cover 1-6-2, the thin-walled ring 1-6-3 and the cylinder flange 1-6-4 adopt a The whole piece of metal material is processed into an integral part of the drive cylinder, and a number of evenly distributed threaded holes 1-6-6 are processed on the cylinder flange 1-6-4, and the threaded holes 1-6-6 are connected with the inner rotor with shaft The output shafts of 2-1 are parallel.
[0015] In this embodiment, the cylinder 1-6-1, the front end cover 1-6-2, the thin-walled ring 1-6-3 and the cylinder flange 1-6-4 are processed into one component, which can reduce energy The purpose of the loss is beneficial to improve the controllability of the vibration trajectory of the surface particle of the drive tooth 1-6-5; the threaded hole 1-6-6 can be used to realize the installation of the motor in the mechanical system.
specific Embodiment approach 3
[0016] Specific implementation mode three: see Figure 4 , the difference between this embodiment and specific embodiment 1 is that each piezoelectric ceramic sheet 1-3 is symmetrically divided into a left half sheet 1-3-1 and a right half sheet 1-3-2, and the left half sheet 1-3-2 The polarization directions of 3-1 and the right half sheet 1-3-2 are opposite, and the two adjacent left half sheets 1-3-1 and the adjacent two right half sheets 1-3 in a pair of piezoelectric ceramic sheets 1-3 The polarization direction of -2 is also opposite.
PUM
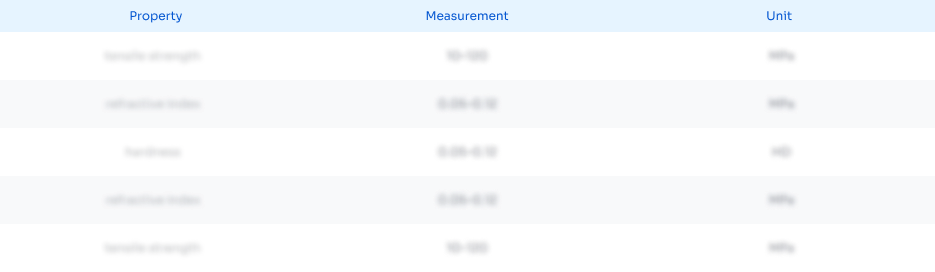
Abstract
Description
Claims
Application Information

- R&D
- Intellectual Property
- Life Sciences
- Materials
- Tech Scout
- Unparalleled Data Quality
- Higher Quality Content
- 60% Fewer Hallucinations
Browse by: Latest US Patents, China's latest patents, Technical Efficacy Thesaurus, Application Domain, Technology Topic, Popular Technical Reports.
© 2025 PatSnap. All rights reserved.Legal|Privacy policy|Modern Slavery Act Transparency Statement|Sitemap|About US| Contact US: help@patsnap.com