Method for controlling vibrating response peak value by memory alloy spring
A memory alloy spring, vibration response technology, applied in the direction of non-rotation vibration suppression, etc., can solve the problems of large space size, unsuitable space vehicle use, heavy weight, etc., to achieve the effect of protection and safety
- Summary
- Abstract
- Description
- Claims
- Application Information
AI Technical Summary
Problems solved by technology
Method used
Image
Examples
Embodiment 1
[0025] Take the chassis circuit board vibration reduction as an example.
[0026] 1. The dynamic load carrying capacity of the circuit board in this embodiment is 35g, and it is determined that the maximum response peak value does not exceed 35g. Since the damping space is less than 10mm, the one side of the damping space is taken as 2.3mm, and the height of the spring is 3.5mm. According to the calculation method of conventional springs referred to in the spring chapter of the mechanical design manual, the relevant parameters of the memory alloy material are input, and the type of spring is preliminarily determined to be the spring leaf configuration.
[0027] A set of memory alloy spring pieces is used to load in the groove, and each spring piece transmits the load evenly. The bearing capacity P of a set of spring pieces is 2.9N. The calculation curve is as follows Figure 7 , represented by three broken lines above O-A, A-B, and B. O-A is simplified to a straight line, wi...
Embodiment 2
[0055] like Figure 8 Shown is the embodiment of the present invention when the precision instrument board is transported and damped.
[0056] 1. According to the dynamic load carrying capacity of the precision instrument board, the maximum vibration peak value is determined to be 1g; the vibration reduction space of the new special transport box is not limited, and it is determined by calculation. According to the calculation method of conventional springs referred to in the spring chapter of the mechanical design manual, the relevant parameters of memory alloy materials are input, and the type of spring is preliminarily determined to be a cylindrical spring configuration that is more convenient for engineering implementation.
[0057] 2. Select memory alloy superelastic cylindrical spring 6. Measure the platform characteristic curve of spring, and revise, calculate the design parameter of spring, as embodiment 1.
[0058] 3. Install selected springs at the four corners of ...
Embodiment 3
[0061] like Figure 9 Shown is the embodiment of the present invention when the whole machine is transported and damped.
[0062] 1. According to the dynamic load carrying capacity of the whole transport machine, the maximum vibration peak value is determined to be 0.6g. Since the damping space is not limited, after installation, refer to the conventional spring calculation method in the spring chapter of the mechanical design manual, input the relevant parameters of the memory alloy material, and initially determine the type of spring as memory alloy superelastic extension spring and superelastic square saddle pad .
[0063] 2. Measure the platform characteristic curve of the spring, and calculate and correct the design parameters of the spring according to the method of embodiment 1.
[0064] 3. After installing the memory alloy superelastic extension spring 10 and the superelastic square saddle pad 13 above the frame, install the whole machine 11 in the vibration damping ...
PUM
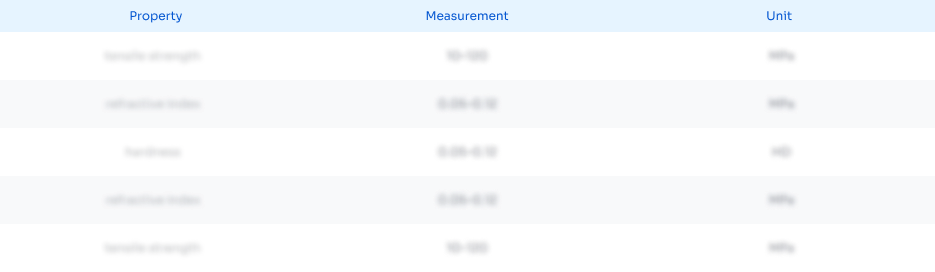
Abstract
Description
Claims
Application Information

- Generate Ideas
- Intellectual Property
- Life Sciences
- Materials
- Tech Scout
- Unparalleled Data Quality
- Higher Quality Content
- 60% Fewer Hallucinations
Browse by: Latest US Patents, China's latest patents, Technical Efficacy Thesaurus, Application Domain, Technology Topic, Popular Technical Reports.
© 2025 PatSnap. All rights reserved.Legal|Privacy policy|Modern Slavery Act Transparency Statement|Sitemap|About US| Contact US: help@patsnap.com