Amplitude frequency spectrum used for mechanical rotor single cross section shaft vibration analysis
A cross-sectional axis and amplitude technology, applied in the field of amplitude spectrum, can solve the problems of inability to reflect the maximum value of the axial vibration component, inconvenient to establish, and inconvenient to compare sensor states, etc.
- Summary
- Abstract
- Description
- Claims
- Application Information
AI Technical Summary
Problems solved by technology
Method used
Image
Examples
specific Embodiment approach
[0037] As mentioned above, the vibration displacement signal is actually measured from a supporting section of a certain rotor, and the arrangement orientation of the X and Y sensors is as follows: figure 2shown. The rotor vibration displacement signals from the X and Y displacement sensors are collected synchronously, that is, the x signal and the y signal, the sampling rate is 2kHz, and the number of sampling points is 1024 points. The specific implementation is as follows:
[0038] (1) Read a group of synchronously collected rotor vibration displacement signals from single-section X and Y sensors of the rotor, that is, x signal and y signal, with a sampling rate of 2 kHz and a sampling point of 1024 points.
[0039] (2) Perform fast discrete Fourier transform (FFT) on the two signal sequences respectively, and the obtained result is a 1024-point complex sequence.
[0040] (3) Based on the fast Fourier transform results of the two signals of x and y, calculate their respec...
PUM
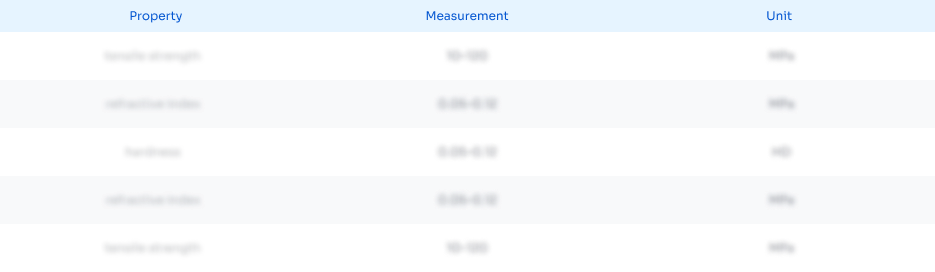
Abstract
Description
Claims
Application Information

- R&D Engineer
- R&D Manager
- IP Professional
- Industry Leading Data Capabilities
- Powerful AI technology
- Patent DNA Extraction
Browse by: Latest US Patents, China's latest patents, Technical Efficacy Thesaurus, Application Domain, Technology Topic, Popular Technical Reports.
© 2024 PatSnap. All rights reserved.Legal|Privacy policy|Modern Slavery Act Transparency Statement|Sitemap|About US| Contact US: help@patsnap.com