Steel works sintering cooling machine low-temperature flue gas residual heat utilization system
A technology for sintering coolers and low-temperature flue gas, which is applied in preheating, waste heat treatment, water heaters, etc., and can solve the problem that the operation parameters of waste heat boilers are difficult to maintain and improve, the actual operating value cannot reach the design value, and the high-temperature section smoke The problem of unstable air temperature can be solved, and the heat recovery rate can be improved, the installation and maintenance are convenient, and the temperature is stable.
- Summary
- Abstract
- Description
- Claims
- Application Information
AI Technical Summary
Problems solved by technology
Method used
Image
Examples
Embodiment Construction
[0039] The technical solutions of the present invention will be further described below in conjunction with the accompanying drawings and specific embodiments.
[0040] According to the present invention and the temperature distribution rule of the sintering blower cooler, the flue gas temperature in the high temperature section is within the range of 300-450°C, and the flue gas temperature in the middle temperature section is within the range of 150-300°C. The flue gas temperature in the middle temperature section is higher than that of the open flue gas system. For this reason, the present invention considers the arrangement of the flue gas system.
[0041] According to a specific embodiment of the low-temperature flue gas waste heat utilization system of sintering coolers in iron and steel plants of the present invention, the system includes a sintering blast cooler with a blower, and the sintering blast cooler passes through a pipeline arranged on its airtight cover It is...
PUM
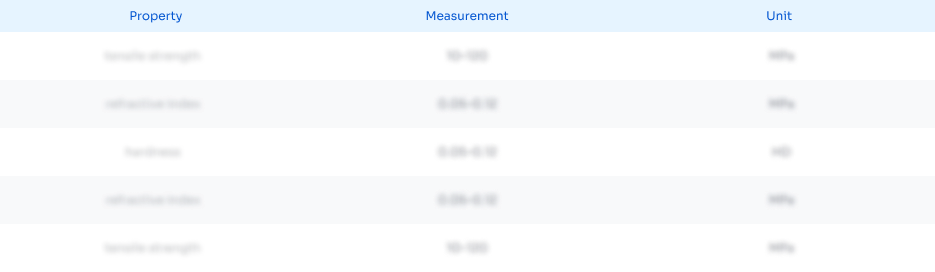
Abstract
Description
Claims
Application Information

- Generate Ideas
- Intellectual Property
- Life Sciences
- Materials
- Tech Scout
- Unparalleled Data Quality
- Higher Quality Content
- 60% Fewer Hallucinations
Browse by: Latest US Patents, China's latest patents, Technical Efficacy Thesaurus, Application Domain, Technology Topic, Popular Technical Reports.
© 2025 PatSnap. All rights reserved.Legal|Privacy policy|Modern Slavery Act Transparency Statement|Sitemap|About US| Contact US: help@patsnap.com