Magnetic rigidity-controlled suspension spring mechanism
A technology of suspension springs and spring devices, applied in the field of coil spring devices, which can solve the problems of being unable to prevent the impact of the suspension system, changing and adjusting the spring stiffness, etc., to achieve the effects of improving work reliability, preventing impact, and avoiding early damage
- Summary
- Abstract
- Description
- Claims
- Application Information
AI Technical Summary
Problems solved by technology
Method used
Image
Examples
Embodiment Construction
[0018] The present invention will be further described below in conjunction with the accompanying drawings and embodiments.
[0019] The magnetic variable stiffness suspension spring device involved in the present invention is composed of a spring upper support, a coil spring, a damping buffer and a spring lower support. The damping buffer is installed inside the coil spring. The present invention is based on the structure of the damping buffer The different forms are divided into three types: upper support type, lower support type and two-way type.
[0020] figure 1 It is a structural schematic diagram of a magnetic variable stiffness suspension spring device, which is composed of a spring upper support 1, a coil spring 5, a spring lower support 10, and a shock absorber 11. The upper end of the coil spring 5 is connected to the spring fixed on the frame The support 1 is connected, the lower end of the coil spring 5 is connected with the spring lower support 10 fixed on the a...
PUM
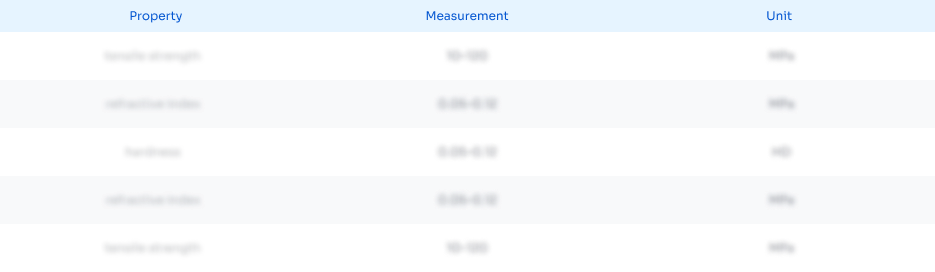
Abstract
Description
Claims
Application Information

- R&D
- Intellectual Property
- Life Sciences
- Materials
- Tech Scout
- Unparalleled Data Quality
- Higher Quality Content
- 60% Fewer Hallucinations
Browse by: Latest US Patents, China's latest patents, Technical Efficacy Thesaurus, Application Domain, Technology Topic, Popular Technical Reports.
© 2025 PatSnap. All rights reserved.Legal|Privacy policy|Modern Slavery Act Transparency Statement|Sitemap|About US| Contact US: help@patsnap.com