Temperature control liquid expanded rubber and preparation method thereof
A technology of liquid expansion and rubber, which is applied in the direction of chemical instruments and methods, drilling compositions, etc., can solve the problems of short validity period, short use time, inability to use deep profile control, etc., and achieve obvious oil increase effect and high output investment The effect of large ratio and outstanding precipitation effect
- Summary
- Abstract
- Description
- Claims
- Application Information
AI Technical Summary
Problems solved by technology
Method used
Examples
example 1
[0051] First, 40% of polyether polyol (POP) is added to the reaction kettle, the temperature is raised to 120 degrees Celsius, dehydrated under vacuum for 30 minutes, the temperature is lowered to 45 degrees Celsius, and 8% of toluene diisocyanate (TDI) is added, and the reaction temperature is controlled at 85 degrees Celsius. Keep warm for 2.5 hours, cool down to 45 degrees Celsius, add 6% xylene, 8.9% phenol, 2% acetone, 0.1% dibutyltin dilaurate, raise the temperature of the reactor to 70 degrees Celsius, keep the temperature for 4 hours, and then add the phenolic resin 20%, 2% natural rubber, 4% xylene, 7% dibutyl phthalate, 1% zinc stearate, add to the reaction kettle, continue to stir for 0.5 hours, cool down to 45 degrees Celsius and add triethylenediamine 1%, stirred for 0.5 hours, cooled to below 40 degrees Celsius and discharged.
[0052] Implementation Effect:
[0053] Plugging effect: The core is made of corundum sand of different particle sizes, cemented with al...
example 2
[0055]Add POP50% into the reaction kettle, raise the temperature to 120 degrees Celsius, dehydrate in vacuum for 30 minutes, cool down to 45 degrees Celsius, add 10% toluene diisocyanate (TDI), control the reaction temperature at 85 degrees Celsius and keep it warm for 2.5 hours, cool to 45 degrees Celsius and add 9% cresol, 2% acetone, 5% xylene, 0.1% dibutyltin diacetate, raise the temperature of the reaction kettle to 70 degrees Celsius, keep it warm for 4 hours, then add 12% phenolic resin, 5% unsaturated resin, o-phthalic acid Add 4% dioctyl diformate into the reaction kettle, stir for 1 hour, cool down to 45 degrees Celsius, add 1% triethylenetetramine, 1.9% zinc stearate, cool down to below 40 degrees Celsius and discharge.
[0056] Implementation Effect:
[0057] Plugging effect: The core is made of corundum sand of different particle sizes, cemented with aluminum phosphate, pressurized, dried, and calcined at high temperature. The core specification and size are Φ25*...
PUM
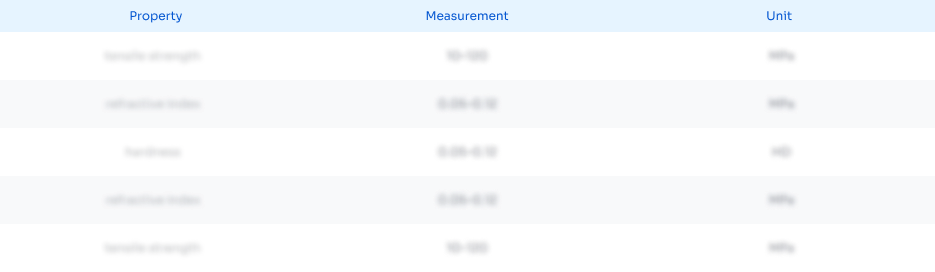
Abstract
Description
Claims
Application Information

- Generate Ideas
- Intellectual Property
- Life Sciences
- Materials
- Tech Scout
- Unparalleled Data Quality
- Higher Quality Content
- 60% Fewer Hallucinations
Browse by: Latest US Patents, China's latest patents, Technical Efficacy Thesaurus, Application Domain, Technology Topic, Popular Technical Reports.
© 2025 PatSnap. All rights reserved.Legal|Privacy policy|Modern Slavery Act Transparency Statement|Sitemap|About US| Contact US: help@patsnap.com