Second-stage reaction process for preparing propenoic acid or ester from lactic acid or ester
A two-stage reaction and acrylic acid technology, which is applied in the preparation of carboxylic acid salts, chemical instruments and methods, and the preparation of organic compounds, etc., can solve the problem of low selectivity of acrylic acid and esters, and achieve the effect of stabilizing the reaction system and improving selectivity
- Summary
- Abstract
- Description
- Claims
- Application Information
AI Technical Summary
Problems solved by technology
Method used
Examples
example 1
[0019] The experiment uses a fixed-bed reactor with 13X molecular sieve as the reaction catalyst. The raw material is 60% lactic acid and methyl ester aqueous solution, 5‰ of p-hydroxyanisole is added, and 2g of 10-100 mesh 13X molecular sieve is weighed. The reaction temperature is 300°C, the vaporization temperature is 235°C, the raw material injection speed is 1.5ml / h, the nitrogen flow rate is 5ml / min, and the product selectivity is 45%.
[0020] The reaction temperatures in Example 1 were respectively set to 275° C. and 325° C., and other experimental conditions remained unchanged, and product selectivities of 21% and 38% were obtained respectively.
[0021] When the raw materials in Example 1 were replaced with 40% methyl lactate, 80% methyl lactate, 60% ethyl lactate, 80% ethyl lactate, 40% lactic acid and 60% lactic acid aqueous solution, other experimental conditions remained unchanged , the selectivities of the products obtained respectively are as follows: 27%, 33%,...
example 2
[0023] The experiment adopts a fixed-bed reactor, and KY molecular sieve is used as the catalyst for the reaction. The catalyst preparation process is shown in the preparation method of catalyst B in (1) above. The raw material is 60% lactic acid and methyl ester aqueous solution, and 5‰ of p-hydroxybenzene Methyl ether, the catalyst loading amount is 2g, the reaction temperature is set to 325°C, the vaporization temperature is 235°C, the raw material injection speed is 2ml / h, the nitrogen flow rate is 10ml / min, and the product selectivity is 43%.
[0024] The reaction temperatures in Example 2 were respectively set to 300° C. and 350° C., and other experimental conditions were kept constant, and product selectivities of 17% and 39% were obtained respectively.
[0025] When the raw materials in Example 2 are replaced with 40% methyl lactate, 60% ethyl lactate and 40% lactic acid aqueous solution respectively, other experimental conditions are constant, and the selectivity of th...
example 3
[0027] The experiment adopts a section of fixed-bed reactor, uses praseodymium phosphate as the catalyst of reaction, the catalyst preparation process sees the preparation method of catalyst C in the above (1), raw material is 60% lactic acid and methyl ester aqueous solution, adds 5% p-hydroxybenzene Methyl ether, the loading amount of the catalyst is 2g, the reaction temperature is set to 325°C, the vaporization temperature is 235°C, the raw material injection speed is 1.5ml / h, the nitrogen flow rate is 10ml / min, and the product selectivity is 40%.
[0028] The reaction temperatures in Example 3 were respectively set to 300° C. and 350° C., and other experimental conditions were kept constant, and product selectivities of 19% and 35% were obtained respectively.
[0029] When the raw materials in Example 3 were replaced with 80% methyl lactate, 60% ethyl lactate and 40% lactic acid aqueous solution respectively, other experimental conditions were unchanged, and the selectivity...
PUM
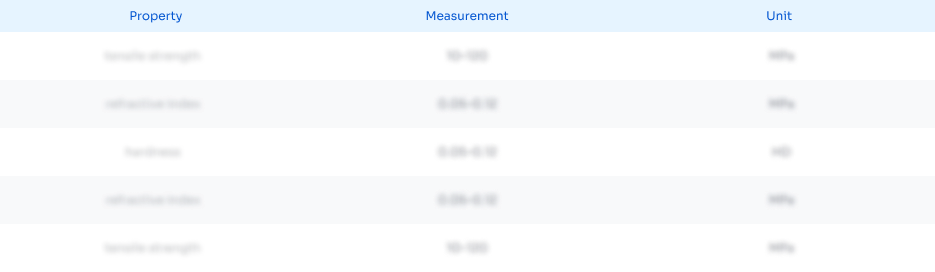
Abstract
Description
Claims
Application Information

- R&D
- Intellectual Property
- Life Sciences
- Materials
- Tech Scout
- Unparalleled Data Quality
- Higher Quality Content
- 60% Fewer Hallucinations
Browse by: Latest US Patents, China's latest patents, Technical Efficacy Thesaurus, Application Domain, Technology Topic, Popular Technical Reports.
© 2025 PatSnap. All rights reserved.Legal|Privacy policy|Modern Slavery Act Transparency Statement|Sitemap|About US| Contact US: help@patsnap.com